|
|
第六节 叠合回转工装及剪切设备 |
|
|
|
制造覆铜板的设备除主要设备上胶系统和压机系统外,还需要配料设备、叠合设备、剪切/测厚设备、工装以及其它很多配套设备,其中叠合、剪切/测厚设备既是不可缺少的设备,又对产品质量起着十分重要的作用。近几年,叠合、剪切/测厚设备技术发展很快,自动化程度还在不断提高,并向灵活性、实用性方向发展。
一、叠合设备
有半自动叠合和自动叠合2种方式。
(一)、半自动叠合
其工作流程大致如图3-6-1所示,配好的PP人工推到配料台边,切好的铜箔也由人工推到台边,再由人工将PP和铜箔组成一个个“没有压制的板”。配好的料再由人工推到叠合(BOOK)机房,在一个升降台上进行组合。抛光板由吸吊车吸到组合台,而配好的料由人工搬运到组合台。这样交错进行,为防止铜箔打皱和清除铜箔表面污物,在组合的同时要用清洁布对铜箔进行扫布,上下铜箔均需扫布。这样“抛光板-铜箔+PP组合-扫布-抛光板-扫布-铜箔+PP组合-扫布-抛光板”循环,叠合成一个个BOOK,手动推到下一个工序:层压。
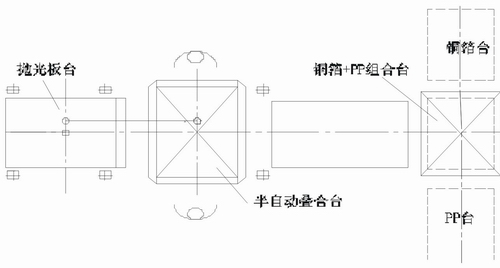
图3-6-1 半自动叠合设备
(二)、自动叠合设备
1. 自动叠合设备组成
如图3-6-2,自动叠合设备由下述机器组成:A1-切下铜箔机 A2-搬运下铜箔机 A3-运抛光板机(带抛光板定位) A4-切上铜箔机 A5-搬运上铜箔机 A6-组成“下铜箔-抛光板-上铜箔”三合一体 A7-组合台 A8-三联吸吊车(见图3-6-3) A9-PP搬运并定位机 A10-分离PP机
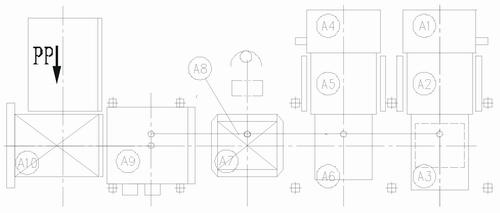
图3-6-2 自动叠合设备
2. 自动叠合之原理
(1)抛光板进到A3台,同时下铜箔切割机切出一张下铜箔由A2搬运到A3位的抛光板上。
(2)切出一张上铜箔至A5,通过A5双排吸嘴将上铜箔搬运至A6位。
(3)A10将交替叠好的PP进行分离,再由A9搬运至A9位,在A9位PP要进行定位。
(4)由A8中1#搬运架将A3位组合好的下铜箔和抛光板从A3位夹住搬运至A6位。
(5)由A8中2#搬运架将A6台上组合好的“下铜箔、抛光板、上铜箔”组合体夹住搬运至A7。
(6)由A8中3#搬运架从A9将PP搬运至A7台,于是完成一个周期,叠好一块板。这样不断循环, A8中1#、2#、3#搬运架是联在一起的,三个架同时动作。当完成组合系统所需的张数后,自动叠合一个BOOK完成,由A7组合台出BOOK。

图3-6-3 三联吸吊车
二、洗板机
洗板机(见图3-6-4)主要功能是将抛光板上的尘粒和粘附物质磨掉,再用水清洁抛光板,进行烘干后,进入组合间进行组合。它由磨板区、洗板区、烘板区三大部分组成。
(一)、磨板区 由2只(或4只)直径超过Ф300的磨辊(抛光板上下各一根)组成。磨辊压紧在抛光板表面上高速转动,将抛光板上的尘粒磨掉,磨的同时需往磨辊上喷水,带水磨板既可以减少磨辊负载,同时水又可以带走磨辊掉下来的磨粒和从抛光板磨下来的尘粒。
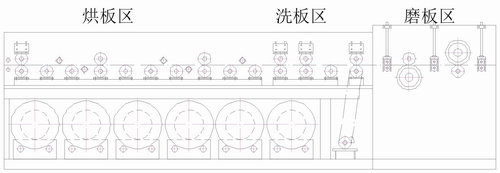
图3-6-4 洗板机
(二)、洗板区 其功能是将磨好的板清洗干净。抛光板进入此区,先由一组上下刷辊在高压水喷射下,对抛光板进行刷板,再由一组经过高效过滤的水枪对抛光板喷射,将抛光板表面完全清洗干净。
(三)、烘干区 由上下各一组“风刀”组成,最后一组风刀是热风。当抛光板进入此区,“风刀”高速吹向抛光板,将抛光板吹烘干净。之后抛光板进入净化间,进行BOOK自动叠合。
三、剪切/测厚设备
剪切/测厚有手动和自动2种方式,采用自动剪切/测厚方式是一种趋势。
(一)、手动剪切和测厚
手动剪切用非金属剪床,它是由一把锐角上刀、一把直角下刀、驱动、定位铁、放板台及压紧机构组成。操作人员将板放在平台上,通过定位铁将板定位后,人工操作剪切动作,完成板的一条边剪切,要剪好一块板需剪切四次。剪切好的板,由人工用千分尺测厚或者用单一操作头的接触式测厚仪对板进行测厚。目前常用的剪板机规格是3×1500mm,整机为标准型。只是上、下刀片要特制加工(图3-6-5)其剪切倾角为30′~38′,前角20o,后角12′。
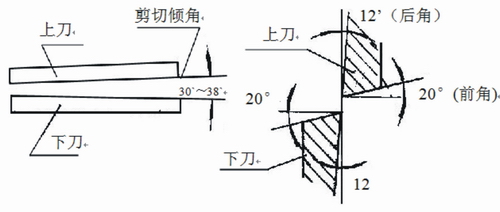
图3-6-5 剪板机刀片剪切角
如果要求覆铜板成品机加工尺寸精度高、断面整齐,必须采用锯铣机对成品加工。
锯铣机如图3-6-6所示。其功能可满足工艺加工尺寸的精度要求。使用时需配套通风除尘、除渣设备,该机比剪板机加工尺寸精度高,断面整齐,有利于板材的自动化生产。
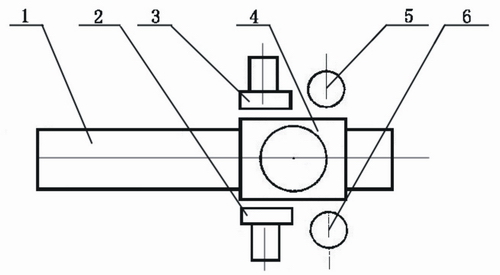
1-移动床身;2、3-圆盘锯;4-旋转工作台;5、6-铣边机
图3-6-6 锯铣机
(二)、自动剪切/测厚设备组成及工作原理(见图3-6-7)
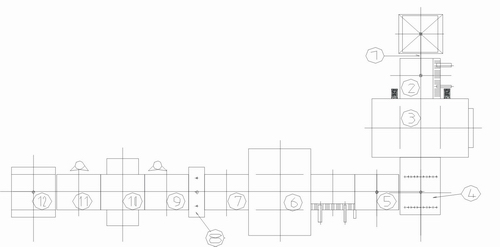
图3-6-7 自动剪切/测厚设备
C1.吸吊车――将产品吸到自动剪切线上;
C2.带定位运输带――板在C2处定位,再输送到C3剪切第一刀;
C3.剪床――对板剪切第一刀,剪切方式有裁切和滚剪两种方式。其中裁切可以剪切0.05- 3.2mm的板,但剪切噪音比较大。滚剪只能切0.05-1.6mm的板,这种剪切方式比较平稳,也没有噪音。
C4.转角台――实现板的转向输送。
C5.带定位运输带――在进入C6第二刀前先定位,再将板输送到C6。
C6.剪床――剪切板的另外2条边,性能同C3。
C7.输送带――将C6剪切好的板输送到C8进行测厚。
C8.自动测厚仪――有接触式和非接触式2种。接触式测仪一般采用气缸夹将板压紧,再由光栅探头来探测压板位移来测厚。这种接触式测厚方式比较成熟,但要受测量速度限制,如果测量太快,其精度和稳定性要受到影响。非接触式测厚一般是用镭射探头来测厚,这种测厚经过多年努力,目前技术已经比较成熟。自动测厚的数据可直接录入电脑记录,供质检人员作分析用。
C9、C11.外观检验台――在此处由操作人员看板的正反面,确定板的等级。
C10.翻板――把板的另一面从下面翻到上面以供检验。
C12.板分级――根据C8测厚及C9、C11外观检测结果,在此处对板进行分级,A级板进入堆叠和包装工序。
(三)、手动剪切/测厚与自动剪切/测厚之比较
手动剪切精度受人为因素影响较大,切薄板时板容易打折,操作人员劳动强度大,但具有剪切尺寸和厚度灵活之优点,在某些时候手动剪切是自动剪切不可替换的。手动剪切时一般用手动测厚。
自动剪切自动化程度高,精度一致性好,剪切速度快,在剪薄板时不会折伤板,但自动剪切对原板是有条件限制的。自动剪切时一般用自动测厚。
四、覆铜板用工装
1、抛光不锈钢板
前面提到的抛光板,实际为抛光不锈钢板,有时也称模板。是制造覆铜板必须的工装。其应耐化学物质的腐蚀,要有适当厚度,足够的刚性和硬度,还要有良好的传热性,并能承受压力和温度的冲击,有良好的光洁度,以保证覆铜板的层压面的外观质量,俗称镜面板。覆铜板用不锈钢板可按表3-6-1、3-6-2选用。
表3-6-1 覆铜板用不锈钢板化学成分和力学性能表
序号
|
钢 材 牌 号 |
2Cr13 或 X20Cr13 或 SuS420J |
SUS630
|
供 应 状 态 |
淬 火 |
时效处理 |
1 |
机械强度Mpa
|
σ s |
400 ~ 500 |
1420 |
σ b |
1380 ~ 1550 |
1430 |
2 |
延伸率 σ s % |
78 |
|
3 |
硬度 洛氏 HV |
480 |
≥ 340 |
4 |
导热系数λ(20℃)/(w/km) |
30 |
40 |
5 |
热膨胀系数α(10-6·K -1)
|
20 ~ 100 ℃ |
10.5 |
10.9 |
20 ~ 200 ℃ |
11.0 |
11.4 |
20 ~ 300 ℃ |
11.5 |
11.5 |
6 |
化学成分%
|
C |
0.20 |
0.02 |
Si |
0.60 |
0.3 |
Mn |
0.60 |
0.8 |
Cr |
13.00 |
16.5 |
备注:1)淬火:1000℃急冷-200℃回火
2)时效处理:450℃均热2小时
表3-6-2 纸基覆铜板用不锈钢板规格尺寸表
序号 |
规格尺寸 mm |
用途 |
1 |
1050 +1.65 × 1050 +1.65 × 1.5 ± 0.10
对角长度: 1484.92 +2.00
|
在压机上压制 1020 × 1020 覆铜板
|
2 |
1250 +1.65 × 1050 +1.65 × 1.5 ± 0.10
对角长度: 1632.48 +2.30
|
在压机上压制 1220 × 1020 覆铜板
|
注:①.平行度≤0.05mm,平面度≤0.03mm/M,表面粗糙度为
②.不锈钢板工作表面在正常的自然光线下或在75瓦灯光下、光源与工作表面间距0.5M条件下,目测不应有渣、麻(锈)点、气(针)孔、压坑、划痕等表面缺陷,并要求不锈钢板周边倒圆角。
2、托板和盖板
应选用≥4mm厚的SUS304板材或TU-430全硬化钢,在要求不高的产品中,可用冷轧板代替。托板尺寸由设备制造厂提供。盖板尺寸没有明确规定,原则上是每边较模板大3—5cm为宜。
五、钢板运输设备
1. 钢板运输车
此车适用于小批量生产,如图3-6-8所示。
1-防滑木块; 2-车
图3-6-8 钢板运输车
2. 钢板运输回转线
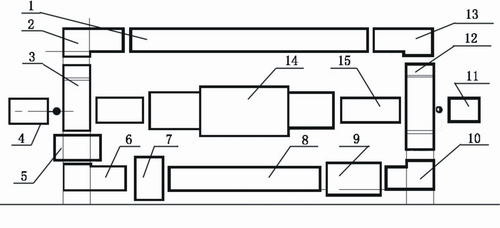
1-托板线;2、6、10、13-转角机;3、12-移板机;4-装料机;5-去边碴机;7-去边碴机;8-模板线;9-钢板清洗机;11-成品运输车;14-热压机;15-链式输送机
图3-6-9 钢板运输回转生产线
图3-6-9所示的钢板运输回转生产线,是自动化程度较高的生产线中采用的一例。
(1)优点
能半自动化生产,劳动强度可以大大减轻;能自动清理模板及残渣,确保产品质量;防止人为划伤模板,可延长模板使用期限;模板堆放整齐,工作场地整洁。
(2)缺点:需要投资大。工房面积要大,维修复杂,还必须配套除尘设备(保证残渣的清理)
|
|
|
|
|
|
|
热点新闻 |
|
|
|