|
|
第五章 覆铜板用主要原材料
第一节 铜箔(三) |
|
|
|
五 铜箔质量控制
1 铜箔厚度的控制
首先来讨论电解铜箔的厚度问题。铜箔的厚度有标称厚度和机械厚度两种说法。通常所述的厚度一般是指标称厚度,即铜箔的单位面积质量,也就是我们通常所说的标重或者基重。铜箔的厚度控制,一般是通过控制毛箔的基重和表面处理沉积量来控制的。毛箔的基重是通过电流和阴极转速来控制的。固定的生产电流下,转速越高其基重越小,反之亦然。粗化层的大小和形状,是由表面处理工艺决定的,具体来讲主要由粗化和固化步骤决定的。至于采用的是粗-粗-固-固模式,还是粗-固-粗-固模式,有一定的区别不是十分严格。另外,在粗化中使用特殊的添加剂会明显改变粗化层的形状。表面处理对铜箔厚度的调节主要是粗化和固化两个步骤,一般是通过调节电沉积量来调整的,而过渡层、锌铬层的影响很小,可以忽略不计。对于一般的HTE铜箔,不管是一般用途的常规型FR-4还是High-Tg型FR-4、Halogen-free型FR-4,表面处理后铜箔的标重一般会增加8~15g/m2,机械厚度一般会增加2-4μm。对于FPC用铜箔,表面处理后一般会增加5~14 g/m2,例如LED灯条用的1oz黑色LP型铜箔,表面处理增加5g/m2左右就能够满足抗剥离强度要求。对于标重相同的铜箔,表面粗糙度大的铜箔,一般其机械厚度也偏大。
对于多数铜箔生产者而言,控制铜箔的基重并不是困难之事,难点是控制铜箔的均匀度,即单点厚度要做均匀,这是下游更关心的问题。通常,控制铜箔的单点均匀性有两种常见的方法,即阳极屏蔽和极间流速控制。无论是铅阳极还是钛阳极(包括弧形和FIP条两种),随着使用周期的延长,阳极腐蚀会导致电流分布不均,造成局部厚度异常。对于铅阳极来讲,阳极腐蚀产生的硫酸铅还会影响阳极电位和电流分布,导致电沉积速度的变化,引起局部厚度和粗度的改变。对于钛阳极,它的表面涂覆有一层特殊的二氧化铱层,比较有利于电流分布和降低阳极的电极电位,容易得到均匀度良好的铜箔,同时还会提高电流效率。
对于某一规格的产品,其厚度的一致性控制,通常采用测量单位面积质量、机械厚度、表面Rz、SEM、切片等多种方法来调控的。单一的测试方法有时很难评价铜箔的一致性是好还是差。IPC-4562标准中规定的基重偏差±10%,是粗略了一些。当然它只是最基本的要求,客户的需要才是真正的标准。对于标重,实际生产中一般可以控制在±5%以内,甚至更低一些的水平,这需要对毛箔和表面处理层进行严格的控制。CCL业有关专家曾提出采用金相显微切片法对铜箔厚度进行评价,则是个比较准确的方法。但由于业内没有形成统一的标准,或者是实践中因为某些因素不便于作业,故没有推广,一般和客户出现争议时才会用到。遇到这样的问题时,我们习惯的做法是在超景深显微镜下进行观察,取最大峰高,多测几个点,同时结合铜箔表面的SEM或3D图像进行观察分析。需要说明的是,这种非在线、非连续的检测,被测铜箔样品仍然属于抽样方式,有时并不能完全反映铜箔品质的好坏,良好的铜箔品质一定是高精细化的管理来保证的。
2.铜箔RZ的控制
表面粗糙度Rz,又称微观不平度十点高度。其定义为:在取样长度内5个最大的轮廓峰高平均值与5个最大轮廓谷深平均值之和。
Rz只能反映轮廓峰的高低,不能反映峰顶的尖锐或平钝的几何特性,同时若取点不同,则所得Rz值不同,因此受测量者的主观影响较大。电解铜箔表面的Rz,主要由毛箔的峰值和粗化层决定。要求毛箔的“山峰”要有一定的高度且均一,而表面处理层能够满足抗剥要求即可,粗化层的展开度应该适当的做小、粗短一些。在实际的生产中,工程技术人员应该高度管控电解添加剂的使用量,以及与过滤的匹配问题。得到峰值均匀的毛箔,是高性能铜箔的关键步骤之一。
其次是在表面处理的粗化中可以使用添加剂,这些添加剂在粗化铜的枝状沉积过程中起到阴极阻化的作用,会形成更多的生长点,使粗化层向“山谷”方向生长,这样得到的铜箔Rz较小,但抗剥离强度较高(如图1中b所示),而不使用添加剂一般会得到图1中a所示的状态,粗化层在峰顶上生长。

图5-1-13 35μm铜箔粗化层结构示意
Rz值大,容易导致PCB蚀刻残铜。主要是因为毛箔峰值不均和粗化层过大引起的。毛箔的山峰不均,会导致个别山峰的粗化层异常增大(图1中f所示),容易在PCB的电路制作中造成局部蚀刻不净。粗化层过大(如图1中c所示),铜瘤不牢固。在压合过程中可能会受到剪切,铜牙易脱落,易造成PCB线间短路。在制作薄型化覆铜板时,铜牙扎入深度大,板材的绝缘性能会严重下降,当然,粗化层过小则容易导致抗剥离强度偏低。从线路制作的角度来讲,应该将Rz做到小一些,均匀一些。近年来,特别是大屏幕PDP,液晶LCD,平板显示器FPD等用到的精细线路铜箔(厚度多在10μm左右),表面处理层更要求高度的均一(如图2)。
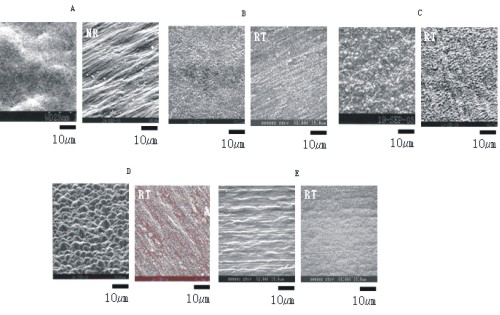
图5-1-14 精细线路用铜箔的SEM比较
对于HTE铜箔,明胶(Glue)和HEC(羟仪基纤维素)是电解过程中常用的添加剂,用它们来调节,一般情况下厚度越大,Rz越大。对于双面光锂电池铜箔来讲,因添加剂不同,厚度较大,Rz反而容易做小。FPC用VLP铜箔,使用特殊的添加剂,9~70μm铜箔可以做到Rz都在1.5~2.5μm范围内。而对于大功率使用场合的超厚铜箔(3oz以上),加入平整剂将Rz控制到7~12μm的范围内,完全是产业化。
那么,究竟是将铜箔毛面Rz做的高一点好,还是低一点好?这要依据使用的场合而定,一般来讲只要抗剥离强度能够满足使用要求,Rz值还是低一点较好,均匀一些好。
3 铜箔软硬度的控制
铜箔的软硬,一般可以通过测试抗拉强度来判断。铜箔的抗拉强度分为常温(23℃)和高温(180℃)两种表示方式,主要是通过调节添加剂的使用量来控制的。对于HTE铜箔,随着明胶的使用量增大,常温抗拉强度升高后会再迅速下降,铜箔变硬后变脆,高温抗拉强度则在缓慢升高后趋于水平。同时,伴随着常温延伸率升高,高温延伸率急剧下降,Rz降低,山峰趋于均匀;随着HEC使用量的增加,铜箔的常温抗拉强度会降低,高温抗拉强度变化不大,Rz会降低。需要说明,山峰变得平坦,容易导致表面处理后抗剥离强度降低。我们的工程技术人员,需要观察铜箔实际生产状况调节添加剂的匹配量,寻找一个平衡点,使铜箔的软硬适当,延伸率合格,Rz适中,山峰尖锐而均匀。对于双面光锂电池铜箔和FPC用VLP铜箔,光亮剂、平整剂、Cl-和活性炭的匹配十分重要,抗拉强度和延伸率是负线性相关的。要求较高抗拉强度的同时,延伸率又很高,需要使用特殊的混合添加剂,如S-HTE型VLP铜箔就是这种情况,12μm的常温抗拉强度能够达到450MPa以上,高温抗拉强度可以达到220 MPa以上,常温、高温延伸率均达到8%左右的水平。
不管是HTE箔、锂电池铜箔,还是FPC用箔,其抗拉强度稳定性和一致性是很重要的。抗拉强度的一致性,反映了制程控制的连续性和稳定性,尤其是对于FPC用箔表现的更为明显,只有抗拉强度稳定了,延伸率和前面讲过的Rz才会稳定,铜箔的抗剥离强度才会稳定。
4 铜箔延伸率的控制
铜箔延伸率的控制与前述抗拉强度控制基本一致。前面,我们提到了抗拉强度与延伸率负线性相关。调节明胶、HEC、Cl -和活性炭的匹配量,也就控制了铜箔的延伸率。对于目前国内的铜箔厂都能生产HTE铜箔,延伸率的控制也不是问题,其重点还是生产管理问题,最重要的就是过程稳定。
5 铜箔剥离强度控制
铜箔的抗剥离强度(Peel Strength,简称PS)影响因素主要有以下几点:(1)毛箔的粗糙度Rz、峰的尖锐性和均匀性。(2)粗化层的形状与大小。(3)硅烷偶联剂的种类和涂覆量。(4)树脂基材的类型。(5)压板工艺状况。(6)测试条件等因素。
毛箔的粗糙度Rz越大、峰越尖锐、均匀性越好,表面处理后的铜箔的抗剥离强度越高;粗化层越大(瘤状颗粒越多,越大),展开度越大(最高的是45°),PS越高。
硅烷偶联剂的种类和涂覆量,与树脂的匹配很关键,环氧基板一般使用环氧基的KH560,酚醛基板常用氨基的KH550。当然也有使用改性的混合硅烷偶联剂,效果也很好。
树脂基材的类型对PS影响相当大。近年来,PCB技术飞速发展,很多环境、条件、方法已经不同于过去,技术的进步给材料应用带来一系列要求。例如,微小孔加工时,为了获得良好的孔壁质量,PCB制程采用更快的钻孔速度,会带来孔壁过热问题;多层板反复压合,由于基材与铜箔膨胀系数存在差异,可能会造成线路铜裂;板材加工过程中热风整平,以及元件焊接被无铅焊接工艺取代,经过多次热冲击后,易出现孔壁拐角铜裂及孔壁收缩等问题;高密度安装技术条件下,板材的尺寸稳定问题;环境安全对卤素阻燃剂的限制。鉴于此,各CCL厂致力于提高板材的耐热性,并降低膨胀系数(CTE)和无卤化。往往会采用高耐热性的高分子固化剂,配合多官能团树脂改性的环氧树脂使板材具有高Tg和耐热性;另外添加适量的无机填料(常用硅微粉),来降低膨胀系数;使用无机阻燃剂(常用氢氧化铝)来替代卤素。但就是在追求其高Tg、低CTE、无卤素的同时,使得基材树脂对铜箔的接合力降低,一般的FR-4型CCL采用35μm(1oz)铜箔的 PS 能够达到2.0N/mm(11.4 lbf/in),而Tg值为150℃左右的Halogen-free FR-4型CCL板采用35μm铜箔的PS值,只能达到1.4 N/mm(8 lbf/in)左右。压板时的压力、温度、时间等参数对树脂的交联效果影响很大,会直接影响到PS的高低。
目前,国内铜箔的技术水平,大都能够满足中Tg 的无卤素板材使用水平,而应用在Tg为170℃以上的板材PS值还是不够,其技术难点在于低Rz的毛箔,山峰均匀而尖瑞,表面处理的粗化层向山谷生长,而且颗粒饱满(如图3所示),普通的表面粗化技术和一般的设备条件无法达到。图3给出了一种具有优良粗化层结构的35μm铜箔,满足上述高性能CCL要求。
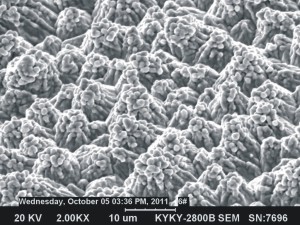
图5-1-15 优良粗化层结构的35μm铜箔
对于FPC用VLP铜箔的抗剥离强度,除了受粗化层结构(如图4)影响之外,硅烷偶联剂的影响也不能忽视,它存在一个与胶水的兼容问题,通常情况使用环氧基的偶联剂会好于氨基的偶联剂,而使用混合偶联剂更好。 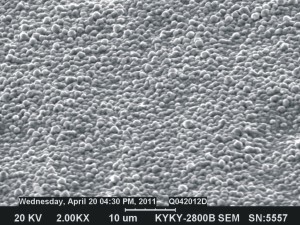
图5-1-16 18μm FPC用S-HTE型VLP铜箔
在实际的生产控制中,并不是PS越高越好,PS太高有可能会造成残铜现象,因此只要能够满足客户使用要求就是最好的。
6 铜箔耐化学性控制
铜箔在PCB制程中应该具有一定的耐化学腐蚀性,应该包括光面和毛面两个部分。
对于铜箔的毛面,一般是和树脂粘合的一面,耐腐蚀性过强会导致蚀刻不净,PCB制作时会发现基材变暗,线路基板的绝缘性较差。耐腐蚀性过弱,则容易出现线条侧面腐蚀现象,严重的会造成线条脱落。关于这一点,当然也存在铜箔与基材匹配的问题。抛开与基材匹配,单从铜箔的生产过程来分析,无论是耐腐蚀性过强,还是过弱,大都与表面处理有关。一般来讲与M面过渡层、耐高温层的厚度和比例有关,与防氧化膜也有一定的关系。通常状况,过渡层、耐高温层、防氧化膜一般是镀一层很薄(约50纳米)的铜-砷合金,或者是锌镍合金、钴钼合金、铜-氮合金、铜-锑合金,或镀镍、镀钴等超微细的结晶,再加锌铬酸盐防锈。几种盐膜厚度比例,会影响铜箔的耐化学药水性,不管是酸性还是碱性蚀刻工艺,都有一定的影响。通常,镀层中的镍含量越高,其碱性蚀刻性就越差。
过渡层与耐高温层的厚度比值越大,耐腐蚀性越强,相反,则越差。至于是红化箔还是灰化箔,只是镀锌层的厚度不同而已,锌含量达到100ppm以上时镀层变为灰色。因为灰化铜箔锌含量较高,要求过渡层作用更强,所以我们发现灰化铜箔在普通FR-4板上的耐盐酸劣化率很小,但在Halogen-freeFR-4型CCL或High-TgFR-4型CCL上的劣化率会略高一些。铬酸盐的含量会影响到铜箔的存放,沉积量控制在10~50ppm的范围,含量越高,耐腐蚀性越强,相反会变差一些。
铜箔的光面,一般只有一层电析出附着的锌铬盐防氧化膜。防氧化膜的厚度,在PCB中的主要表现在可能会对微蚀和湿法贴膜有一定的影响。薄膜增厚,耐腐蚀性增强,容易出现H2SO4-H2O2(或过硫酸钠,Na2S2O8)蚀刻条纹或贴膜不牢。PCB制程可以通过延长微蚀时间、升高温度等措施解决,但可能会影响效率。是不是可以把光面的镀层做薄一些呢?答案也不能,因为减少薄膜的厚度会影响光面的抗氧化性,高温抗氧化性也会降低。现在客户要求FR-4铜箔在200℃,通风状态下,60min以上不氧化,锌铬盐含量过低时会牺牲铜箔的防氧化性能。
7 铜箔毛面颜色控制
铜箔毛面的颜色实际上对PCB在蚀刻方面没有什么影响。不管是什么颜色的铜箔,CCL和PCB厂家希望铜箔生产商能够在颜色上保持稳定。但客户还是喜欢颜色深一点的红化铜箔,因为它更容易满足线路制程中的AOI检测,特别是适用于一些早期的AOI检查机,其分辨率较低。主要因为,FR-4板基材部分比较透明,蚀刻线路后可以清晰地看到另一面铜箔的毛面颜色,浅颜色的粉红色铜箔,容易产生误判报警。
对于铜箔生产者来说,毛面颜色的稳定状态,反映的是生产制程的控制水平。颜色不一致,可以认为是生产中某一方面控制波动。一般来讲,影响铜箔的毛面颜色的主要因素有:(1)毛箔Rz的大小;(2)峰的均匀性;(3)粗化层的状态;(4)盐膜的沉积量和比例;(5)溶液控制范围;(5)溶液控制范围;(6)表面处理电流控制范围。
毛箔毛面的Rz越大,单位面积内的山峰数目越少,粗化处理后铜箔的比表面积越小,同等表面处理条件下沉积量越少,颜色表现为变浅;毛箔山峰的均匀性差,同理也容易处理成浅色粗化面;而粗化层的展开度越大或者粗化层越高,颜色容易变深。
中间层沉积量增大,铜箔的颜色也会变暗,并有向黄铜色转变的趋势。因为镀层会扩散,对颜色感官造成一定的影响,分为两种情况:自然转化和高温转化。在自然存放条件下,镀层金属扩散,毛面颜色会有变化:红化铜箔会变的略红,灰化箔会变为灰黄色,黑化箔会变的更黑。高温转化比自然转化更为迅速、彻底,影响压板后的颜色。一般客户判断颜色都是以压板后的颜色作为管理依据。
颜色控制的难点在于:稳定的电解工艺,包括铜离子、硫酸浓度的稳定水平,温度、流量、活性炭、添加剂的匹配能力。还有,电解液的管理水平,保持高度纯净的电解液至关重要,因为杂质离子或有机物的存在会改变铜的结晶取向,影响到铜箔的延伸率、粗糙度等进而影响表面处理后的颜色。当然表面处理过程,要求各个步骤的溶液稳定是比较难的,自动控制水平越低,越困难,因此一定要加强自动化水平,单靠人工控制是不行的。
8 铜箔抗氧化性控制
铜箔的抗氧化性,分为常温和高温两种状态,通常观察光面的抗氧化性。不管是什么用途的铜箔,其正反两面都会有一层起保护作用的盐膜。一般来讲,在钝化盐膜中锌量越高,铜箔的抗高温氧化性越强,铬量越高,常温存放能力越强。结合前面,我们提到的耐化学药水问题,锌铬膜的沉积量必须控制在适当的范围内。低了,会影响抗氧化性,高了,会影响蚀刻性。至于常温抗氧化能力,是6个月还是9个月,要依据具体的存放环境而定。铜箔存放环境干燥还是潮湿,是内陆还是靠近海洋,都会有一定的影响。铜箔的抗常温氧化性较差,会形成黑色的小点,这样的点在PCB制造过程中可以通过PCB加工过程中微蚀或磨板步骤去掉,但由于影响CCL的外观,厂家一般不愿接受,因此铜箔生产厂就必须适当地提高铜箔的抗常温氧化性,增加盐膜的沉积量,在抗氧化性、蚀刻性和可焊性之间寻找最佳平衡点。对于铜箔的高温抗氧化能力,锌的沉积量越高,铜箔耐高温能力越强,但过多的锌有导致铜箔耐盐酸劣化率性能下降的风险。
实践中通过抽样检测其抗氧化性,从而来控制调控相关工艺条件。
9 铜箔表观的控制
铜箔常见的表观缺陷有:(1)针孔、渗透点;(2)凹坑、麻点、划伤;(3)褶皱;(4)黄点、蓝点、红点等四大类型。
针孔和渗透点是电解毛箔的过程中产生的。针孔是透光的直孔,渗透点是疏松的镀层形成的曲孔,一般都是由微小的颗粒状杂质引起,杂质在阴极表面吸附,影响了晶核的形成,或是引起了析氢电位的变化造成过饱和氢气泡的析出而形成。
凹坑属于铜箔受外界力的作用,局部变形的情况,主要由于生产环境的净化不良造成。麻点一般是因为铜箔的峰值不够均匀,由较大山峰或结晶缺陷等引起的局部挤压造成的轻微变形,没有形成凹坑,但光面几何尺寸有微小变化,光泽度变化了,隐约可以看见小点。
划伤一般是外界因素造成的铜箔蹭伤或磨伤。一般提高净化和加强过滤会得到解决。褶皱有两种类型,一种是在外界力的作用下铜箔发生的形变而生成,一般为设备的导辊不水平或不平行或者张力不均造成。另一种暗纹或由横向均匀性不一形成的,也能看得出,但这种暗纹一般不影响使用。
至于黄点、蓝点和红点大多是在表面处理的过程中形成的,一般与通风条件有关,不影响内在性能,通过微蚀或刷磨是可以清除的,但是CCL厂家不会允许铜箔有已知的缺陷存在。就像IPC-4562标准,规定允许多大面积内有多大,多少个点、坑、划伤等缺陷,实际上已经没有什么意义,客户的要求就是标准。
总之,除了以上要求,客户还有翘曲、接头数量、卷重、标识等其它方面的要求,虽然很繁琐,但是很必要。我们要做的只有不停地改进、改进、再改进。只要能做到的我们都应该努力做到。PCB产品朝着精细化的方向发展,客户会越来越要求铜箔“零缺陷”。由于铜箔在生产中的控制环节很多,很复杂,很容易出现波动,以至于目前国内企业都还无法达到“零缺陷”,但追求产品的“零缺陷”和客户的高满意度一定是我们不懈奋斗的目标!
在铜箔市场竞争日趋激烈的今天,只有依靠技术创新,不断的改进与提升现有产品的质量水平,才能满足客户的各种需求。同时,积极的开发新产品,开拓新型市场,提高产品的技术水平,才能提升企业的竞争优势。
定型产品的质量状态,靠的是精良的设备、先进的工艺和优秀的管理。而研发新产品和开拓新市场,需要的不仅是优秀的技术团队,更要有热情服务客户的态度和不断追求卓越的精神,这才是企业发展的不竭动力和源泉。
|
|
|
|
|
|
|
热点新闻 |
|
|
|