一、铜箔分类与技术标准
(一)铜箔分类
随着电子信息技术的发展,对覆铜板用铜箔在品种及质量上都提出了很多更新更高的要求,促使铜箔技术更快发展,使铜箔品种及规格不断增多,产品档次及技术要求不断提高。
1.按生产工艺划分
根据其生产工艺的不同,可分为压延铜箔(rolled-wrought copper foil)和电解铜箔(electrodeposited copper foil)。
压延铜箔是将铜先经熔炼加工制成铜板,再将铜板经过多次重复辊轧制成原箔,然后根据要求对原箔进行粗化处理、耐热层处理及防氧化处理等一系列表面处理。由于压延铜箔加工工艺的限制,压延铜箔的幅宽很难满足刚性覆铜板的生产要求,所以压延铜箔在刚性印制电路板(RPCB)上使用很少。但是由于压延铜箔属于片状结晶组织结构,因此在延伸率、耐折和高温重结晶等方面要优于电解铜箔,所以压延铜箔大多用于挠性印制电路板(FPC)上。此外,由于压延铜箔的致密度较高,表面较为平滑,利于制成印制电路板后的信号快速传送,因此在高频电路、精细线路的印制电路板上也使用一些压延铜箔。
电解铜箔是以电解铜或具有与电解铜同等纯度的铜线等为原料,在硫酸中溶解制成硫酸铜溶液,在直流电作用下,在筒状阴极表面电沉积金属铜并持续剥离制成原箔。然后根据要求对原箔进行粗化、耐热及防氧化等一系列表面处理。电解铜箔不同于压延铜箔,电解原箔两面表面结晶形态不同,紧贴阴极辊的一面比较光滑,称为光面(S面)。另一面呈现凹凸形状的结晶组织结构,比较粗糙,称为毛面(M面)。传统的印制电路用电解铜箔属柱状结晶组织结构,其延伸率、耐折和高温重结晶等性能要逊色于压延铜箔,所以长期以来电解铜箔多用于刚性覆铜板的生产,而压延铜箔多用于挠性覆铜板。近几年,随着电解铜箔生产技术的提高,许多铜箔厂家已经开发出适合于挠性印制电路板、高频电路板、微细电路用的电解铜箔,这些特殊用途电解铜箔的延伸率和耐折性已经十分接近同规格压延铜箔,表面粗糙度也控制在特定的范围,个别品种的挠性印制电路板用电解铜箔也具有一定的高温重结晶性。由于电解铜箔生产技术的提高和价格方面的优势,越来越多的挠性印制电路板、高频电路板和微细电路板生产厂家开始使用电解铜箔代替压延铜箔。
2.按性能划分
按其性能可分为:标准铜箔、高温高延伸性铜箔、高延展性铜箔、耐转移铜箔、低轮廓铜箔、超低轮廓铜箔等。
(1)标准铜箔(STD):主要用于压制纸基酚醛树脂覆铜箔层压板和环氧玻纤布覆铜板(以普通FR-4板为代表),对于用于纸基覆铜板的铜箔,为了提高铜箔与基材的结合强度,在对铜箔进行粗化处理后,还要涂一层专用胶,这种铜箔的粗化面粗糙度比较大,铜箔厚度一般在18~70μm,各种性能要求不是很高。对于用于玻纤布覆铜板的铜箔,除了进行必要的粗化处理外,还要进行耐热处理(如镀镍、钴、锌等的合金)、特殊耐高温防氧化处理,与基材有较高的结合力,耐热温度达到200℃左右,它以18 μm铜箔为主体。
(2)高温延伸性铜箔(HTE):主要用于多层印制板(Multi-layer circuit board)上,由于多层印制板在压合时的热量会使铜箔发生再结晶现象,需要铜箔在高温(180℃)时也具有较高的延伸率,以保证内层线路不出现“铜裂”现象。随着多层线路板产量和技术水平的提升,对电解铜箔高温延伸率性能的要求有了大幅提高,IPC-4562标准规定HTE铜箔的高温延伸率大于3%的要求已成为最低标准, 通常所说的HTE铜箔,是指高温延伸率在5 %以上的12-35μm电解铜箔。
(3)高延展性铜箔(HD):主要用于挠性线路板上,要求具有很高的耐折性能,因而它要求必须具有很高的致密度,并进行必要的热处理过程。
(4)耐转移铜箔:主要用于绝缘要求比较高的印制板上,如果铜箔压制成线路板后,发生铜离子转移,则对基板的绝缘可靠性会造成相当大的影响,因此必须对铜箔表面进行特殊处理(如镀镍等),以抑制铜的离子化及进一步转移。
(5)低轮廓铜箔(LP):主要用于多层印制线路板、高密度电路板上,它要求铜箔表面粗糙度比普通铜箔小,而抗剥离强度等性能保持较高的水平,属于一类特殊的控制粗度的电解铜箔。
(6)超低轮廓铜箔(VLP): 主要用于挠性电路板、高频线路板和超微细电路板,它的表面近乎于平滑,粗糙度通常在2 μm 以下。一般电解铜箔的微结晶表面比较粗糙,具有明显的晶体取向,呈粗大的柱状结晶,其切片横断层的棱线,起伏较大。而VLP铜箔的结晶很细腻,为等轴晶粒,不含柱状的晶体,呈成片层状结晶,且棱线平坦。
3.按照厚度还可以分为常规厚度铜箔(18-70μm)、薄铜箔(12-18μm)、超薄铜箔(8-12μm)、极薄铜箔(1-8μm)、厚铜箔(70-105μm)、超厚铜箔105-500μm。
需要说明的是,通常所说的多少微米铜箔一般都是以单位面积质量来区分的,并不是铜箔的实际测量厚度。
4.按表面处理颜色,电解铜箔可以分为红化、灰化、黑化几种典型的颜色类型。
(1)红化铜箔:电解铜箔的表面经过粗化层处理后,电镀一层铜、镍、钴、钼等金属的合金作为阻挡层,再电镀一层很薄的锌和铬,铜箔的表面呈粉红色或红褐色。其中最常见的阻挡层是电镀一层超微细铜砷合金,但由于生产中的安全和产品的环境危害问题,铜砷合金逐渐被电镀镍、钴、钼、钨等金属的锌合金层替代,防氧化层为镀锌或镀锌铬合金。目前,铜箔生产厂家都使用锌或锌合金来提高铜箔的抗高温氧化性,几乎都是使用铬酸盐钝化。由于红化铜箔的表面耐热层很薄,所以其高温抗氧化等性能一直以来都要逊色于灰化铜箔。近几年,红化铜箔的表面处理技术更新很快,其高温抗氧化性能有了很大提高,几乎所有性能都可以和灰化铜箔相媲美。
我国是电子铜箔的生产大国,但在技术水平上与日本、韩国及中国台湾还有较大的差距,造成了国内的高性能电解铜箔长期依赖进口的局面。近年来,国内铜箔的生产技术有了很大程度的提高,越来越多的国产铜箔被使用到高端PCB产品上,但由于高档PCB用铜箔市场长期以来被进口铜箔占领,而且这些进口铜箔近乎都是红化铜箔,所以在CCL生产商的思维中形成了一种固有的颜色需求,于是红化铜箔的市场需求量在迅速增加,国内的众多铜箔生产厂家也都在大力研究高性能的红化铜箔。
(2)灰化铜箔:电解铜箔的表面经过粗化层处理后,电镀一层铜、镍、钴、钼、铁、钨等金属的合金作为阻挡层,再电镀一层锌合金作为耐热层并使用铬酸盐钝化,铜箔的表面呈银灰色或灰褐色。铜箔的表面呈灰色是电镀铁系(铁、钴、镍)或锌合金的颜色,镀层的厚度控制在适当的范围,过厚时铜箔的耐药品腐蚀性下降,过薄时铜箔抗高温氧化性和颜色会有明显改变。
(3)黑化铜箔:电解铜箔的表面经过粗化层处理后,电镀一层镍、钴、铜、钼、铁、锌等金属的合金,再电镀一层防氧化层,铜箔的表面呈黑褐色或纯黑色。铜箔的表面呈黑色的原因是上述镍、钴、铜、钼、铁、锌等金属的合金层,通过特殊的工艺形成的硫化物、氧化物或其他共溶性黑色化合物。黑化铜箔通常使用VLP铜箔作为基础箔,经过黑色表面处理后用于挠性覆铜板和电磁屏蔽材料。
(二)铜箔技术标准
1.国内外主要铜箔技术标准介绍
(1)日本铜箔技术标准(JIS)
日本目前采用的铜箔技术标准有:JISC6512《印制电路板用电解铜箔》和JISC6513《印制电路板用压延铜箔》,分别于1992年和1996年颁布实施。 JISC6512铜箔标准共涉及三种电解铜箔:标准电解铜箔,型号为ECF1;常温高延展性电解铜箔,型号为ECF2;高温延伸性电解铜箔,型号为ECF3。JISC6513铜箔标准共涉及三种压延铜箔:冷压延铜箔,型号为RCF1;轻冷压延铜箔,型号为RCF2;退火压延铜箔,型号为RCF3。JISC6512和JISC6513标准分别对电解铜箔和压延铜箔的主要技术要求作了规定,其中包括:光面和粗糙面的外观、针孔、尺寸、质量厚度及偏差、铜纯度、质量电阻率、铜箔光面粗糙度、抗拉强度及延伸率等指标。
1998年10月,JIS-C-6512、6513均改订、合并为JIS-C-6515。
(2)国际电工委员会有关铜箔的技术标准(IEC)
国际电工委员会颁布的现行有效的铜箔技术标准是IEC1249-5-1《制造覆铜板基材用铜箔》,该标准同样涉及六种铜箔,其中电解铜箔三种:分别是标准电解铜箔、常温高延展性电解铜箔、高温高延展性电解铜箔,型号分别为E1、E2、E3。还有压延铜箔三种:压延铜箔、轻冷压延铜箔、退火压延铜箔,型号分别为W1、W2、W3。该标准对电解铜箔和压延铜箔的技术要求主要包括:单位面积质量、厚度、铜纯度、机械性能、电性能、铜箔两面粗糙度、尺寸及偏差等指标。
(3)IPC有关铜箔的技术标准(IPC)
IPC于1966年对印制电路用铜箔制定了IPC-MF-150A《印制线路用金属箔》标准,此后又陆续修改制定了其升级标准B.C.D.E.F等,到1999年又制定了IPC-MF-150G,而到2000年IPC又制定了IPC-4562《印制线路用金属箔》标准,完全替代了IPC-MF-150G及其以前版本的标准。IPC-4562标准规定了目前所有用于印制电路的金属箔技术要求,其中共涉及十种铜箔(包括六种电解铜箔和四种压延铜箔),该标准不但涉及的铜箔品种多于JIS标准和IEC标准,而且技术要求也比JIS和IEC标准要求更多更细更严格。因此,IPC-4562《印制线路用金属箔》成为目前国际通用的印制电路用铜箔技术标准。
(4)我国铜箔技术标准(GB)
我国于1995年制定了GB/T5230-95《电解铜箔》国家标准,其中只包括标准电解铜箔和高延展性电解铜箔这两种。显然已经不能满足需要,于是在2000年全面修改并制定了新的铜箔国家标准GB/T5230《印制线路用铜箔规范》,该标准等效采用了IPC-4562标准,涉及到的铜箔品种已达到九种,对铜箔的技术要求包括:单位面积质量及其偏差、尺寸及偏差、抗拉强度、延伸率、质量电阻率、铜纯度、可焊性、针孔及渗透点、铜箔光面粗糙度及处理面的表面质量等指标。这些技术要求同GB/T5230-95相比,规定得更细更严。
表5-1-1 国内外铜箔品种及型号对照表
铜箔品种 |
型号 |
IPC4562
(2000 年) |
GB/T 5230
(2000 年) |
JIS C 6515
(1992 年) |
IEC 1249-5-1
(1995 年) |
标准电解铜箔 |
STD-E |
E-01 |
ECF1 |
E1 |
高延展性电解铜箔 |
HD-E |
E-02 |
ECF2 |
E2 |
高温延展性电解铜箔 |
THE-E |
E-03 |
ECF3 |
E3 |
退火电解铜箔 |
ANN-E |
E-04 |
/ |
/ |
低温退火电解铜箔 |
LTA-E |
E-05 |
/ |
/ |
压延铜箔 |
AR-W |
W-01 |
RCF1 |
R1 |
轻冷压延铜箔 |
LCR-W |
W-02 |
RCF2 |
R2 |
退火压延铜箔 |
AN-W |
W-03 |
RCF3 |
R3 |
可低温退火压延铜箔 |
LTA-W |
W-04 |
/ |
/ |
可退火电解铜箔 |
A-E |
W-05 |
/ |
/ |
(5)欧盟RoHS指令
欧洲议会和理事会2003年1月23日第2002/95/EC号,关于在电子电气设备中限制使用某些有害物质指令(Restriction of Hazardous Substances,ROHS),已成为欧盟立法制定的一项强制性标准,该标准已于2006年7月1日开始正式实施,主要用于规范电子电气产品的材料及工艺标准,使之更加有利于人体健康及环境保护。该标准的目的在于消除电机电子产品中的铅、汞、镉、六价铬、多溴联苯和多溴二苯醚共6项物质,标准规定电子电气设备中禁用物质的最高限量:镉为0.01%(100 ppm),铅、汞、六价铬、多溴联苯和多溴二苯醚为0.1% (1000 ppm)。RoHS指令涉及的产品范围相当广泛,几乎涵盖了所有电子、电器、医疗、通信、玩具、安防信息等产品,它不仅包括整机产品,而且包括生产整机所使用的零部件、原材料及包装件,关系到整个电子行业的生产链。
RoHS指令的实施,对整个铜箔行业带来了一次技术革命,这主要表现在两个方面:一是铜箔生产的环保化。必须禁止直接使用或以杂质的形式从原材料带入上述禁用物质到产品中,为满足市场需求就必须研发新工艺。二是RoHS指令实施后,PCB厂家为适用无铅焊和无卤板需求而研发的新产品,这些新产品对铜箔生产厂家提出了更高要求,为适应客户要求,铜箔生产厂家就必须推出无铅焊和无卤板用铜箔产品。
2.铜箔质量分级
IPC-4562标准及GB/T5230(2000年版本)标准均对印制电路用铜箔按照特性的质量保证水平的分别将其分为三级,在等级之间有代表性的交叠,在多数情况下,各等级之间的差别在于其品质保证水平上,而不是品质的差别。用户应明确他的产品属于那个等级,以便对铜箔的选用提出适当的要求。三种等级如下:
1级:适用于要求电路功能完整,而机械性能和外观不重要的应用场合,此级材料没有规定检查和试验要求。
2级:适用于电路设计、工艺及规范符合要求而允许局部区域有不一致的应用场合。此级材料有中等程度的质量保证,规定了检查和试验要求。
3级:适用于要求保证等级最高的应用场合。
这三种等级中,3级的质量保证水平最高,2级的质量保证水平适中,1级的质量保证水平最低,这一点应特别加以注意。
3.铜箔技术要求
IPC-4562《印制线路用金属箔》及GB/T5230《印制电路用金属箔规范》(GB/T5230等效采用IPC-4562)对印制电路用铜箔提出了详细的技术要求。主要包括:
(1) 尺寸要求:单位面积质量、厚度、长度、宽度及其偏差范围、铜箔表面轮廓值等。
(2)物理性能:抗拉强度、延伸率、疲劳延性、光面粗糙度、剥离强度等。
(3) 加工性能:可蚀刻性、可焊性、处理完善性等。
(4) 工艺质量:铜纯度、质量电阻率等。
(5) 外观要求:表面清洁度、凹点及压痕、皱褶、划痕、缺口及撕裂、针孔及渗透点等。
下面就以IPC-4562及GB/T5230为依据对上述各主要技术指标作简单介绍。
(1)尺寸要求
a.铜箔单位面积质量应符合表5-1-2的规定。
表5-1-2 铜箔单位面积质量
标称厚度μm |
单位面积质量 g/m2 |
IPC-4562 代号OZ |
GB/T5230 代号μm |
允许偏差 % |
5.1 |
45.1 |
E |
5 |
电解铜箔
≤± 10
压延铜箔
≤± 5 |
8.5 |
75.9 |
Q |
9 |
12.0 |
106.8 |
T |
12 |
17.1 |
152.5 |
H |
18 |
25.7 |
228.8 |
M |
25 |
34.3 |
305.0 |
1 |
35 |
68.6 |
610.0 |
2 |
70 |
102.9 |
915.0 |
3 |
103 |
137.2 |
1220.0 |
4 |
137 |
171.5 |
1525.0 |
5 |
172 |
205.7 |
1830.0 |
6 |
206 |
240.0 |
2135.0 |
7 |
240 |
342.9 |
3050.0 |
10 |
343 |
480.1 |
4270.0 |
14 |
480 |
b.电解铜箔的厚度应符合上表中标称厚度的±10%范围内,而对其中的标准轮廓铜箔,没有最大厚度要求。
c.压延铜箔的厚度应符合上表中标称厚度的-5% ~ +10%范围之内,而对其中的标准轮廓铜箔,没有最大厚度要求。
d.片状铜箔的长度和宽度由供需双方商定,其偏差值标准规定为±3.20mm,当然也可由供需双方商定。
e.卷状铜箔的宽度由供需双方商定,其偏差值标准规定为±1.60mm,当然也可由供需双方商定。
f.铜箔轮廓应符合表5-1-3规定。
表5-1-3 铜箔轮廓
铜箔轮廓 |
最大轮廓值μ m |
S (标准) |
无规定 |
无规定 |
L (低轮廓) |
10.2 μ m |
0.4mil |
V (甚低轮廓) |
5.1 μ m |
0.2mil |
(2)物理性能
a.抗拉强度、延伸率、疲劳延性指标对于电解铜箔和压延铜箔及其各品种的铜箔均有不同的要求,供需双方应执行标准规定指标或协商确定。
b.铜箔光面的表面粗糙度算术平均值应不大于0.43μm 。
c.剥离强度并非完全由铜箔决定,还与基材所用树脂种类质量有关。此指标一般由供需双方在明确基材树脂种类质量基础上协商确定。
(3)加工性能
a.经过表面处理的铜箔及其处理层均应能够按正常的蚀刻工艺除去,并且要求均匀一致。
b.铜箔压制成板材后,其铜箔表面应具有良好的可焊性。
(4)工艺质量
a.铜箔在未经表面处理前的原箔,其铜纯度应达到电解铜箔≥99.8%,压延铜箔≥99.9% 。
b.电解铜箔的质量电阻率应达到表5-1-4的要求。
表5-1-4 电解铜箔的质量电阻率
IPC-4562 代号 OZ |
GB/T5230 μ m |
最大质量电阻率(Ω.g/m2) |
E |
5 |
0.181 |
Q |
9 |
0.171 |
T |
12 |
0.170 |
H |
18 |
0.166 |
M |
25 |
0.164 |
10Z 及以上 |
35 μ m 及以上 |
0.162 |
c.压延铜箔的质量电阻率应符合表5-1-5规定。
表5-1-5 压延铜箔的质量电阻率
IPC-4562 型号 |
GB/T5230 型号 |
最大质量电阻率(Ω.g/m2) |
AR 型 |
W-01 |
0.160 |
LCR 型 |
W-02 |
0.155 — 0.160 |
ANN 型 |
W-03 |
0.155 |
LTA 型 |
W-04 |
0.160 |
(5)外观要求
a.不应有直径大于1.0mm的凹点和压痕;每300×300mm区域内,直径小于1.0mm的凹点和压痕不应超过2个,深度小于铜箔标称厚度5%的凹点和压痕可以忽略不计。
b.不应有永久变形性质的皱褶。
c.不允许有深度大于铜箔标称厚度20%的划痕,在每300×300mm 区域上,不允许有多于3条的划痕,小于铜箔标称厚度5%的划痕可以忽略不计。
d.不应有缺口和撕裂。
e.表面不应有灰尘、污物、腐蚀物、盐类、油脂、指印、外来物及其它影响铜箔使用寿命、加工性能及外观的缺陷。
f.对于18μm铜箔,每300×300mm区域上,针孔及渗透点不应超过5个,大于18μm的铜箔,每300×300mm区域上,针孔及渗透点不应超过3个,小于18μm的铜箔标准无规定,由供需双方商定。
g.良好的光面微蚀特性。该性能要求是近几年薄板市场迅速发展后新增的性能要求,对于印制电路板用铜箔,压制成覆铜板经过微蚀(硫酸-双氧水或过硫酸铵微蚀液)后,铜箔的表面不应有点、杠、条纹等异常。
二、电解铜箔制造过程及原理
(一)电解铜箔制造工艺过程
电解铜箔自二十世纪三十年末开始生产后,被用于电子工业,随着电子工业的发展,电解铜箔的品质在不断提高,其制造技术也在快速发展,各铜箔生产企业及相关研究单位对电解铜箔制造技术的研究也取得了相当大的进步,形成多家多种电解铜箔制造技术,各企业生产电解铜箔的关键技术千差万别,但作为电解铜箔制造的工艺过程都大致包括电解液制备、原箔制造、表面处理、分切加工以及相关的检测控制、附属配备等工序。基本工艺流程如图5-1-1所示。 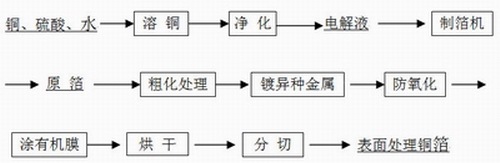
图5-1-1 电解铜箔制造工艺流程
(二)电解液制备
电解液制备是电解铜箔生产的第一道工序,主要就是将铜料溶解成硫酸溶液,并经一系列过滤净化,制备出成分合格、纯净度很高的电解液。电解液质量的好坏,直接影响着铜箔产品品质的好坏,不但影响铜箔的内在质量,还影响铜箔外观质量。因此,必须严格控制溶铜造液过程所用的原料辅料,还要严格控制电解液制备的生产设备和操作过程。
作为制备电解液过程,所用的原料有电解铜、裸铜线、铜元杆、铜米等。要求原料含铜纯度必须达到99.95%以上,铜料中各种杂质如Pb、 Fe、 Ni 、As、 Sb、 Al、 S及有机杂质等必须符合一号电解铜国家技术标准GB466、GB467。生产高品质铜箔时,电解铜最好选用符合GB/T 467-1997中Cu-CATH-1标准的高纯阴极铜或符合GB/T 3952-1998中T1、TU1标准的电工用铜线胚。
硫酸做为一种重要的材料,生产过程中必不可少,其质量应要达到国家标准GB T534-2002工业硫酸技术要求。
1.几种常见的电解液制备工艺流程
(1)流程一(见图5-1-2)。
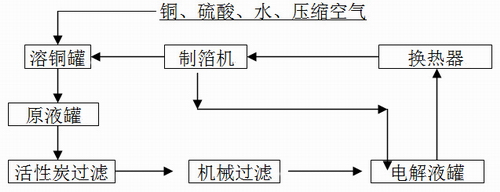
图5-1-2 电解液制备工艺流程一
(2)流程二(见图5-1-3)。
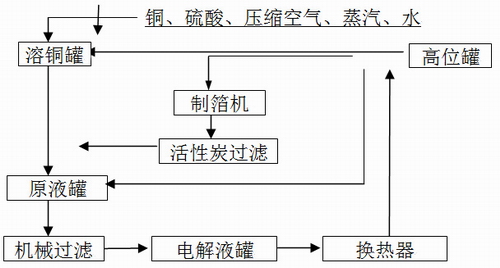
图5-1-3 电解液制备工艺流程二
(3)流程三(见图5-1-4)
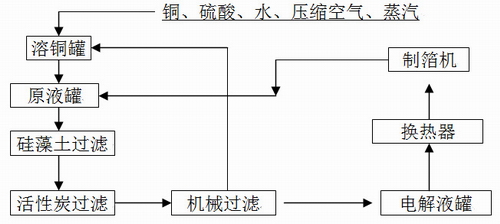
图5-1-4 电解液制备工艺流程三
(4)流程四(见图5-1-5)
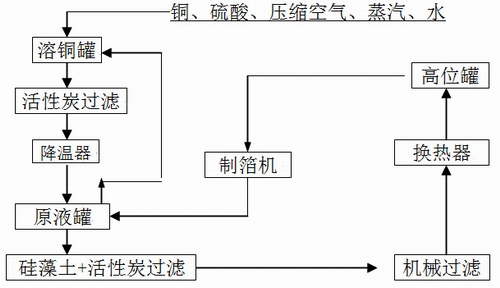
图5-1-5 电解液制备工艺流程四
2.电解液制备过程
上面仅列举了四种有代表性的电解液制备工艺流程,除此之外,由于各铜箔生产企业技术水平、设备条件、配套能力等区别,以及生产铜箔档次要求的不同,在电解液制备循环方式上都有一定的区别。虽然电解液循环方式不同,但其机理都是一样的,都包含有铜料溶解、有机物去除、固体颗粒过滤、温度调整、电解液成分调整等作用和目的。
首先将经过清洗的铜料及硫酸、去离子水加入到具有溶解能力的溶铜罐中,向罐内鼓入压缩空气,在加热(一般为45~90℃)条件下,使铜发生氧化,生成的氧化铜与硫酸发生反应,生成硫酸铜水溶液,当溶解到一定Cu2+浓度(一般为120~150g/L)时,进入原液罐(或经过滤后再到原液罐),与制箔机回流的贫铜电解液(一般为70~100g/L)混合,以使电解液成分符合工艺要求,然后再经过一系列活性炭过滤、机械过滤、温度调整等设备及过程后,把符合工艺要求的电解液送入制箔机(或称电解机组)进行原箔生产制造。
在实际生产过程中,电解液都是循环使用的,不断的从制箔机中生产原箔,消耗电解液中的铜,而由溶铜罐不断溶铜,再经一系列过滤、温度调整、成分调整后,不断送入制箔机。这其中,利用硅藻土和活性炭吸附掉电解液中的有机物(包括有机添加剂及其分解物),机械过滤滤掉(截留)电解液中的固体颗粒物。
电解制备过程不但要保证电解液连续不断地循环,还要及时调整并控制好电解液成分(含铜、含硫酸浓度)、电解液温度、循环量匹配等技术指标。
3.电解液制备主要工艺参数
电解液工艺指标是一个非常重要的参数,在很大程度上决定着电解铜箔质量,决定着溶铜造液的能力和电解液制备所用的设备规格和数量,而电解液各工艺指标之间不是独立的单一参数,而相互制约,相互之间必须匹配。表5-1-6列举一些有代表性的工艺参数,供参考。
表5-1-6 工艺参数
指标名称 |
企业 A |
企业 B |
企业 C |
企业 D |
企业 E |
溶铜罐风压 Pa |
0.12 |
0.1 |
0.12 |
0.1 |
0.15 |
溶铜罐温度 ℃ |
60 |
80 |
85 |
80 |
48 |
溶铜罐含铜 g/L |
90 |
130 |
135 |
140 |
120 |
溶铜罐循环量 m3/h |
50 |
5 |
10 |
8 |
30 |
电解液罐含铜 g/L |
90 |
95 |
90 |
85 |
80 |
电解液罐含酸 g/L |
100 |
95 |
98 |
95 |
120 |
高位罐液温 ℃ |
55 |
55 |
58 |
52 |
--- |
硅藻土、活性过滤次数 |
一次 |
一次 |
二次 |
三次 |
一次 |
机械过滤次数 |
一次 |
一次 |
二次 |
三次 |
一次 |
机械过滤精度 μ m |
1 |
1 |
0.5 |
0.5 |
0.5 |
4.电解液制备的辅助条件
电解液制备所要具备的辅助配套条件包括:铜料处理、压缩空气供给、蒸汽供给以及硫酸和纯水的供给等。
(1)铜料处理
前面提到作为电解铜箔生产所用的原料就是铜料,其中包括电解铜、裸铜线、铜元杆、铜米等。外观要求清洁无油、无有机物、无污物、无其他金属附带等各种有害物质,生产的电解铜箔厚度越薄、档次越高,要求铜料的质量越高,尤其是要求杂质含量越低越好,铜纯度越高越好,附带的有机物越少越好。
铜料特别是电解铜在装入溶铜罐前要剪切成条状或块状,并且要经过碱洗、酸洗、水洗,以去除表面的油污、灰尘等杂物。将铜料剪切成条状或块状的目的是增加铜料的表面积,增加铜的溶解反应速度,可在较低温度下将铜溶解,节省溶铜过程中的能耗。
(2)硫酸供给
硫酸在电解铜箔生产过程中是一种消耗材料,其质量好坏会对铜箔外观及内在质量产生很大影响。因此要选用硫酸国家标准中工业纯或化学纯级以上的品质,纯度≥95%,特别是要确保无汞、铅、镉、铁等杂质不超标。储存硫酸的容器最好选用耐酸加厚工程塑料容器,不要采用碳钢或不锈钢。
(3)压缩空气供给
向溶铜罐内供给的压缩空气,主要作用有两个:一是供给氧气,以促使溶铜罐内有充足的氧,使铜氧化,达到铜溶解的目的;二是提供搅拌作用,促进溶铜罐内铜液流动,提高溶铜速度。所用设备有两种:一是空气压缩机;二是罗茨风机,但无论采用哪种设备,都要求所产生的压缩空气必须无油,还要经过除油、除尘装置,以确保进入溶铜罐的压缩空气纯净。
(4)纯水供给
在电解铜箔生产的全过程都要用到纯水,主要用于初始配液和生产中的液量消耗补充。作为电解液备使用纯水,为防止杂质离子带入电解系统对铜箔的力学性能产生影响,必须使用PH值在6-8,电导率在10-4 S/cm数量级的纯水。目前生产纯水的方式很多,如电渗析、反渗透、离子交换等。作为电解铜箔生产用水,最好采用离子交换或反渗透方式生产,以保证水的纯度和电导率。
(5)作为电解液制备还需要具备蒸汽供给能力。用于给溶铜罐内电解液加温,还必须具有引风装置,用于排放溶铜设备中所产生的酸雾。铜箔生产中常使用酸雾净化塔来处理溶铜和电解过程中产生的酸气,酸雾净化塔的原理是采用过量的氢氧化钠(NaOH)溶液与酸雾(H2SO4)发生中和反应:
NaOH+ H2SO4→Na2SO4+ H2O
使排放到空气中的气体几乎完全是水蒸气,对环境不造成污染。
5.铜溶解基本原理
电解液制备就是将预处理好的铜料投入到溶铜罐中,在硫酸水溶液(电解液)中,通入氧气,经过一系列氧化反应过程,最终形成硫酸铜水溶液,化学方程式如下:
2Cu+O2+2H2SO4=2CuSO4+2H2O
该溶铜反应属固—液、固—气、液—气的多相反应。反应速度与铜溶罐内铜量(确切说应该是铜表面积大小)、氧气供给量、电解液温度反应物在铜料表面界面处的浓度都有重要关系,所以反应速度与反应物接近界面的速度和生成物离开界面的速度、以及界面两相反应的速度都有关系。其中最慢的一步骤决定整个反应速度。在多相反应中,扩散常常是最慢的步骤。多相反应速度还与界面的性质、界面的几何形状、界面的表面积大小以及界面上有无新相生成有关。作为铜溶解的过程,可以大致分为以下几个步骤:
(1)反应物O2、H2SO4扩散到铜料表面;
(2)反应物O2、H2SO4被铜料表面所吸附;
(3)在铜料表面发生化学反应;
(4)生成的CuSO4从铜料表面解吸;
(5)生成的CuSO4通过扩散离开铜料与电解液界面。
上述过程中(1)、(5)两步是扩散过程,(2)、(4)两步是吸附过程,(3)是化学反应过程。反应的实际速度一般情况下是由(1)、(5)扩散过程决定的。
铜料在溶铜罐中处在阳极电位,表面被处在氧和硫酸的阴极区域所包围,铜料给出电子、氧和硫酸在铜料表面处得到电子,使铜料表面电位高于本身和离子间的平衡电位。即发生如下反应。
阴极反应:
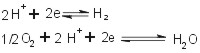
阳极反应:
可见,在铜料发生阳极溶解反应时,阴极发生两种去极化反应,一个是氢的去极化反应,另一个是氧的去极化作用。因此,增大阴极去极化速度就能加快铜料溶解速度。
因此,在实际生产过程中,为加快铜溶解速度须注意以下几点:
(1)尽可能增大铜料表面积,如将电解铜切成小块,使用裸铜线、铜元杆,最好使用铜米。
(2)加大溶铜罐内的鼓风量,其作用有二:一是供给足够的氧气,二是加强搅拌作用。
(3)提高溶铜罐内温度,也有利于化学反应速度和扩散速度,但实验表明当温度达到85℃时,反应速度已经达到最大,所以在实际生产过程中,可以控制80~85℃。
(4)合理布料。就是比较合理地将铜料均匀地布置在溶铜罐中,使压缩空气及电解液都有比较理想的流动通道,有利于提高溶铜速度。
(三)原箔制造
原箔制造是电解铜生产的一道关键工序,原箔就是成品电解铜的半成品,它决定了电解铜箔的大部分质量性能。如铜箔致密度、抗拉强度、延伸率、铜纯度、质量电阻率、针孔渗透点等指标,而且还在很大程度上决定了后道工序表面处理质量的好坏,还是对上道工序电解液制备系统先进性和可靠性的检验。
1.原箔制造的基本过程
原箔制造过程即是一种电解过程。它是在一种专用电解设备中完成的。它一般采用由专用钛材制作的钛质表面辊筒作为阴极辊,采用含银1%铅银合金板或特殊涂层的钛板作为阳极,在阴阳极之间通过硫酸铜电解液,在直流电作用下,阴极辊上便有金属铜析出。随着阴极辊的不断转动,铜不断地在辊面上析出,而不断地将析出的金属铜从辊面上剥离,再经水洗、烘干,缠绕成卷,这就形成了原箔。调节不同的阴极辊转速,就生产出不同厚度的原箔,使用特定的添加剂可以得到不同表面粗糙度和力学性铜的原箔。
2.原箔制造主要工艺参数
作为原箔制造过程中,各生产厂家采用的设备特别是阴极辊区别较大,工艺条件也有很大差异,因此作为原箔制造的主要工艺参数也就有大相径庭,表5-1-7列出几组有代表性的工艺参数供参考。
表5-1-7 工艺参数
参数名称 |
单位 |
企业 A |
企业 B |
企业 C |
企业 D |
企业 E |
Cu2+ |
g/L |
90 |
70 |
95 |
100 |
90 |
H2SO4 |
g/L |
95 |
105 |
120 |
120 |
120 |
电解液温度 |
℃ |
58 |
42 |
52 |
48 |
50 |
总电流 |
A |
15000 |
25000 |
30000 |
40000 |
45000 |
电流密度 |
A/m2 |
6500 |
7000 |
5200 |
8500 |
7800 |
极距 |
mm |
13 |
15 |
15 |
12 |
10 |
液循环量 |
m3/h.台 |
20 |
30 |
40 |
100 |
90 |
槽电压 |
V |
5 |
4.2 |
4 |
5.2 |
5.1 |
洗箔水量 |
m3/天.台 |
8 |
4 |
3 |
12 |
3 |
烘干温度 |
℃ |
70 |
60 |
70 |
85 |
80 |
由此可以看出,各厂家工艺参数区别相当大,这是正常的。但各参数之间都有一定的匹配关系,每个工艺参数的选择及其相互间的匹配关系,决定了原箔的质量优劣。因此,各厂家也在不断地探索合适的工艺参数组合,以寻求最佳的质量和最高的生产效率。
3.原箔制造的辅助条件
作为原箔制造所要求的辅助条件,除了电解液制备及供给外,还需要具备直流供电,阴极辊研磨、电解槽引风和添加剂加入等条件。
(1)直流供电
目前原箔制造所用直流电属于大电流低电压直流电,一般在1000~50000安培。它由一套变压整流设备来提供。
而对制箔机供电的方式有两种:一种是多机串联供电,一种是单机供电,两种供电方式各有优缺点,但目前比较倾向于单机供电,因为它有利于单机操作及单机产品质量调整。
(2)添加剂
电解铜箔的一些特性,如抗拉强度、延伸率、毛面粗糙度、质量电阻率等指标在很大程度上取决于原箔的质量,而要使上述性能达到优良,除了必须供给高纯度的电解液外,还必须向电解液中加入必要的添加剂,如明胶、骨胶、硫脲、聚乙烯醇、淀粉以及一些阴离子和金属盐类等。一般只加入其中的一种或几种。
添加剂的加入方式有两种:一种是直接加入到电解液循环的整体系统中,称为系统加入法;另一种是在电解液进入制箔机前的管道中加入,称为单机加入法。相比之下,单机加入法更好些,但无论采取哪种方式添加,都必须做到添加剂与电解液要充分均匀地混合。
(3)阴极辊研磨
阴极辊的表面质量直接影响电解铜箔光面质量及视觉效果,其研磨技术已成为电解铜箔生产的关键技术之一。在阴极辊研磨这个问题上,各生产厂家所采用的工艺方法区别很大,总的来说,所使用的研磨材料有:各规格砂纸(布)、尼龙轮、尼龙刷轮、PVA轮、研磨绒片、研磨绒盘、绒砂轮、绒片刷等。每个厂家都根据的研磨工艺选用不同的研磨材料。阴极辊研磨可分为下线研磨抛光和在线抛光,所谓下线研磨抛光就是将阴极辊在专用设备上,进行一系列研磨及抛光的过程,在线抛光是将抛光装置安装在制箔机上,阴极辊每生产使用一段时间就对阴极辊辊面进行抛光,这样有利于减少阴极辊装卸次数,提高生产效率。
(4)生产环境:
铜箔生产应选择10万以上的级净化环境,控制温度和湿度。电解铜箔产品的厚度多在8-70μm,空气中微细颗粒可造成铜箔“压坑”废品,特别是生产厚度在18μm以下的铜箔,必须在净化环境中进行。铜箔生产环境温度和湿度对原箔的氧化影响很大,温度、湿度较高的环境原箔容易氧化,氧化较重的原箔经表面处理后的外观质量下降。生产中适用的温度在20-30℃,湿度在50%以内。
4.原箔制造的生产基本原理
原箔制造采用硫酸铜水溶液作为电解液,其主要成分有Cu2+、H+及少量的其他金属阳离子等和OH-、SO42-等阴离子,在直流电的作用下,阳离子移向阴极,阴离子移向阳极,阳极一般采用不溶阳极(铅银合金或涂层钛板等)。由于各种离子的析出电位不同,其成分含量差别较大。在阴极上,Cu2+得到2个电子还原成Cu,在阴极辊面上电化结晶,电极反应如下:

在阴极上OH-放电后生成氧气析出和H+,即: 所以说整个过程还是一个造酸过程。因为氧气跑掉,H+、SO42-结合形成硫酸,即:
总反应为

这样电解液经过该电解过程后,其Cu2+含量不断降低,H2SO4含量不断升高,该过程正好与溶铜过程相反,溶铜过程是使电解液中Cu2+含量不断升高,H2SO4含量不断降低,由此,电解液的循环经过溶铜、电解两个过程来不断维持其中的Cu2+和H2SO4含量,得以平衡。
在电解过程中,Cu2+不断得到电子在阴极辊面上电化结晶,形成原箔,控制各种工艺参数,合理调整阴极辊转速,就能得到不同厚度的铜箔。
对铜箔生产来说,电结晶过程的好坏直接影响到铜箔结晶组织形态,关系到产品的化学成分、电性能、机械性能等。整个电解过程都遵循于电化学原理的法拉第定律、离子迁移理论、电极过程动力学及扩散动力学等。
(四)铜箔表面处理
表面处理是铜箔生产的一个重要环节,它包括对铜箔进行粗化层处理、耐热层处理及防氧化层处理等。其中前二者是在原箔毛面上进行的,而防氧化层处理则是在原箔两面上进行,三个方面处理则在同一台表面处理机上分步骤连续完成
1.表面处理一般工艺过程
目前国内外各铜箔生产企业所采用的铜箔表面处理工艺区别相当大,工艺流程不同,工艺参数也不同,但是应该说都包含粗化、耐热、防氧化三种处理。处理流程,如图5-1-6所示。
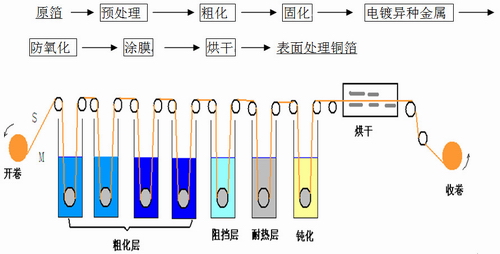
图5-1-6 表面处理流程
(1)预处理
预处理是指对原箔表面进行的清洗,去除氧化及对表面进行浸蚀的过程,原箔在制箔机生产后有较短的存放过程,使得原箔在生产及存放过程中表面很容易产生氧化层,这是在进行粗化处理前必须去除的。另外,某些处理(如对原箔光面进行粗化处理)前,须要对其表面进行必要的浸蚀处理。这些都需要对原箔进行预处理,预处理一般采用硫酸、双氧水等水溶液或其混合水溶液。
(2)粗化层处理
为使铜箔与基材之间具有更强的结合力,需要对原箔的毛面(与基材结合面)进行粗化层处理(如图5-1-7),它包括粗化和固化两个过程。在粗化处理过程中,需要使电解液控制较低的含铜量及较高的含酸量,通过电解作用,在铜箔毛面(阴极)发生铜沉积,在表面形成牢固的粒状和树枝状结晶(如图5-1-8),并且有较高展开度的粗糙面,达到高比表面积,这就加强了树脂(基材上的树脂或铜箔粘合剂树脂)渗入的附着嵌合力,还可增加铜与树脂的化学亲合力。
一般的粗化处理都采用酸性电解工艺方式,即原箔为阴极,在硫酸铜的电解液中通过几次电沉积,通过控制不同的工艺条件(电解液浓度、电流密度、温度等)来对铜箔表面进行粗化及固化处理,使铜箔表面形成松散的瘤体,然后进行固化,使粗化瘤体被正常的铜镀层所包围及加固,在粗化层与铜箔基体结合时更牢固,形成最终的粗化层。
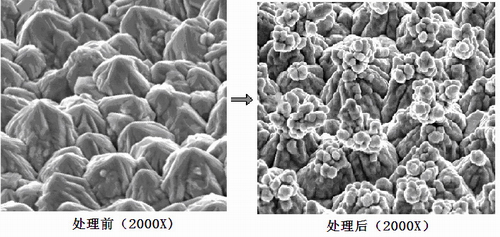
图5-1-7 电解原箔和表面处理后SEM(35μm)
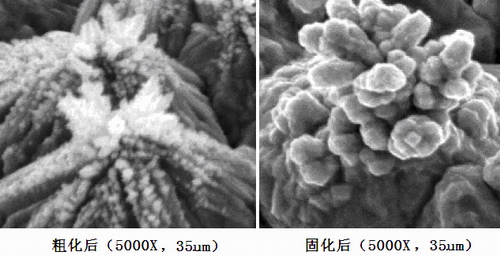
图5-1-8 电解原箔粗化和固化后SEM(35μm)
对于电解铜箔来说,铜箔厚度及用途的不同有很大差别,要求铜箔表面粗化层也不同,有的需要高峰值粗化层,有的需要低峰值粗化层,这就要求铜箔生产过程需要采用不同工艺条件的表面粗化工艺来实现。
(3)耐热层处理
耐热层处理的主要目的是为了提高铜箔压制覆铜板及多层板后的耐热性及高温抗剥强度。这是因为电路板在整机元器件装配焊接时,由于受到高温影响,其树脂中的固化剂双氰胺容易裂解产生胺类物,它与裸铜表面相接触,将发生反应而可能出现水分,进而汽化,引起所泡产生,使铜箔与基板分离。
铜箔的耐热层处理一般是采用电镀锌合金的办法,也就是在铜箔粗化层面上镀一层锌合金,使铜表面不与基材直接接触,避免热冲击后的分层问题。
目前所镀金属一般有:镀一层锌,颜色为灰色,称为灰化处理,此种铜箔叫做镀锌铜箔;镀一层铜锌合金,即黄铜,颜色呈黄色,称为黄化处理,此种铜箔称为镀黄铜铜箔;镀一层镍合金,颜色为黑色,称为黑化铜箔,此种铜箔称为镀镍铜箔。
耐热层处理不但可以阻挡胺类物对铜箔表面的攻击,而且有助于增加铜箔与基村的化学亲合力,进而提高抗剥强度。
(4)防氧化处理
铜箔在储存、运输及压板生产过程中,常会遇到一定湿度的空气及较高的温度,很容易使铜箔表面发生氧化变色,它会影响铜面的可焊性及对油墨的亲合性,并且引起铜箔厚度的微小变化及氧化层的产生,导致线路电阻增大,因此在铜箔生产过程中,就要对铜箔表面进行防氧化处理(有时也称钝化处理,稳定性处理)。
常见的防氧化处理工艺有酸性和碱性两种,都是使铜箔做为阴极,通直流电,使得在铜箔表面形成以锌、铬为主体,结构复杂的碱式铬酸盐防氧化膜,以使铜箔不直接与空气接触,达到防氧化目的。目前,电解铜箔生产商几乎都是采取铬酸盐电镀防氧化膜,而用钼酸盐、钨酸盐以及三价铬的钝化工艺基本上都处于试验阶段,但取代铬酸盐电镀将是一个趋势。
2. FPC、电磁屏蔽、高频电路、精细电路铜箔的表面处理
FPC、电磁屏蔽、高频电路和精细电路用铜箔,属于特殊用途铜箔,通常都是VLP铜箔类型,这些特殊铜箔的表面处理不同于传统的表面处理,一般采用酸性镀铜、镍、铁、钴、钼、钨的合金微细粗化,该粗化是在高电流密度下形成的细小点状结晶,再在较低电流密度下电镀一层镍、钴、钼等的合金作为固化层,形成微小的粒状结构(如图5-1-9),同时起到了阻挡层的作用,再经过镀锌或锌合金的耐热层,最后经铬酸盐钝化,其表面处理流程如图5-1-10所示。这些特殊用途的铜箔,厚度通常在9-12μm,要求具有高度均一的表面和内在特性,表面以黑色较为常见,主要是镀铁系元素(镍、钴、铁)合金呈现的颜色,由于其表面(光、毛面) 很光滑,粗糙度(Rz)通常都小于2.0μm,所以对表面处理设备要求较高,一般的表面处理装置会出现打滑和起折等问题。
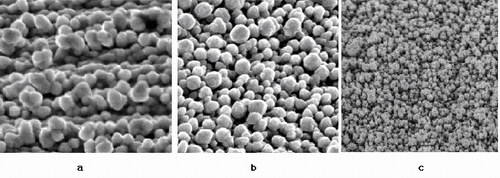
图5-1-9 FPC、电磁屏蔽、高频电路和精细电路铜箔的几种典型表面形态(2000X)
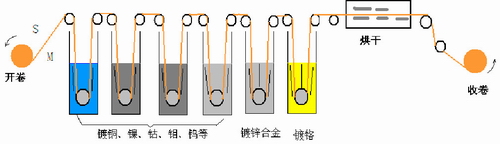
图5-1-10 FPC、电磁屏蔽、高频电路和精细电路用铜箔表面处理
3.表面处理过程中的其他工艺及条件
(1)涂膜工艺
目前在铜箔生产过程中,在对铜箔进行粗化层处理,耐热层处理及防氧化层处理后,一般还要涂覆一层硅烷偶联剂,其作用有两个:一是进一步提高铜箔与基材结合力;二是有利于进一步提高防氧化能力。
硅烷偶联剂是由硅氯仿(HSiCl3)和带有反应性基团的不饱和烯烃,在铂氯酸催化下加成和醇解后得到的一类具有特定性能的有机官能团的硅烷,在其分子中同时具有能与无机质材料(如金属、玻璃、硅砂等)化学结合的反应基团和能与有机质材料(合成树脂等)化学结合的反应基团,通式为Y(CH2)nSiX3,n=0~3;X-可水解基团;Y一有机官能团,能与树脂起反应。X 通常是氯基、甲氧基、乙氧基、乙酰氧基等,这些基团水解时即生成硅醇(Si(OH)3),使用时与铜箔表面镀层结合,形成硅氧烷。Y是乙烯基、氨基、环氧基、甲基丙烯酰氧基、巯基或脲基,能与树脂反应而结合。在铜箔和树脂的界面之间架起"分子桥",把两种性质悬殊的材料连接在一起,增加粘接强度。在硅烷偶联剂的这两类性能互异的基团中,以Y基团最重要、它对制品性能影响很大,起决定偶联剂的性能作用。当Y基团能和对应的树脂相容并起反应时,能提高铜箔在树脂上的抗剥离强度。
在实际的电解铜箔生产中,常选用氨基、环氧基和改性硅烷偶联剂,并以1%-15%的水溶液环境涂覆于铜箔的表面。
(2)水洗
表面处理是一个复杂的多种工艺过程,也是一个连续的生产工艺过程,这其中在各步处理过程中都有必要的水洗过程,以清除表面附带的电解液。对所用的水要求很高,一般均采用离子交换水处理方式。它是采用离子交换树脂,使离子交换树脂中和水溶液中可交换离子之间发生符合等物质量规则的可逆性交换,使水中离子去除而离子交换树脂的结构并不发生实质性变化的一种水处理方式。
对于铜箔漂洗用水和电解液制备用水一般要求电导率应小于10μs/cm。
(3)烘干
烘干是表面处理过程的最后一道必不可少的工序,它的目的是烘干去除铜箔表面的水份,防止残留水分对铜箔的抗氧化性和有机硅烷偶联剂性能的影响。
根据铜箔处理速度的不同,烘干温度也就不同。一般以不低于100℃为原则,也有达到200℃甚至300℃以上的。原则上应完全彻底去除铜表面水分,又不能因温度过高而伤害铜箔。
(4)溶液制备
表面处理过程中的预处理、粗化、固化、镀异种金属、防氧化及涂膜工艺采用的溶液都有一个制备过程。有的采用配制,有的需要采用溶铜方式。这些溶液都需要独立的制备设备、净化设备及温度调节设备,这些做为表面处理工艺过程的配套条件是必不可少的。 |