|
|
第六章 纸基覆铜板 第四节 常见质量问题及解决方法 |
|
|
|
一、耐浸焊性
(一)耐浸焊性的重要性
耐浸焊性,这项性能是目前国内普遍存在的问题。也是许多生产厂家十分注重的工艺技术问题。
电子产品的性能可靠性在相当大的程度取决于印制电路板的质量可靠性,电器部件插装在印制电路板上以后,要进行自动焊接(波峰焊或浸焊)。在这过程中若出现铜箔的起泡,甚至是焊盘、铜箔线条翘起以及导线脱落,除与印制电路板加工工艺不合理有关外,与覆铜板耐浸焊性有关。国内波峰焊的时间和温度的上限为5秒/260℃,通常采用2.5—4.5秒/230—250℃,最佳条件一般在3秒/240℃附近,按照我国国家标准一般纸基覆铜板的耐浸焊性的指标是10秒/260℃,即在10秒以内不分层、不起泡。
提高和稳定覆铜板的耐浸焊性的重要性在于:1、电视机、录音机等大部分的元器件等都插装在印制电路板上,若因板的耐浸焊性差或不稳定,就会使整个元器件以及印制板损坏或报废并影响整个组装生产线正常进行。2、若在自动焊接后未检查出印制板的该质量问题,就会在整机组装后,甚至自动焊接后未检查出印制板的该质量问题,造成更大的浪费和损失。3、有些整机厂发现一些印制板在过波峰焊中出现该质量问题,有时就不得不采取降低焊接温度、降低波峰没入板的深度等措施。使焊料不能充分接触焊盘,焊料流动性差,造成润湿不良的缺陷,导致整机的质量稳定性降低。
各覆铜板生产厂对浸焊性的质量问题是非常重视的。这项性能的稳定与平整度几乎成为衡量同类纸基覆铜板质量的两大敏感性的重要项目。它直接严重影响着各生产厂的产品声誉。
(二)在热冲击条件下,覆铜板“起泡”是界面严重破坏的结果
纸基覆铜板是由溶液或熔融状态的树脂通过上胶(包括对粗化铜箔的涂胶)、压制,与纸纤维增强材料,铜箔固化成型在一起的复合材料,从板的结构看,通过上述加工后,多种组分,就形成多种界面结构。所指的界面,是树脂与纸纤维增强材料的界面,胶粘剂与铜箔的界面,以及树脂和胶粘剂通过热压产生化学反应交联的整体与增强材料、铜箔各为一侧的界面。
当树脂与增强材料固化成一体时,树脂基本会产生收缩,而且树脂与纸纤维、铜箔的热膨胀系数也相差很大,因此,在固化过程中各个界面上就会产生附加应力。另一方面,已固化成型的纸板,也会在外力、受热作用下,产生板内的应力分布不均匀的情况,甚至在界面上某些部位集中了较高的应力。所产生的上述两种应力,会使界面遭到局部的化学键的破坏,引起板的内部材料形成微裂纹。
在制板过程中,残留在板界面的孔隙中的水分子以及一些低分子物也对界面的破坏造成很大的促进。
上述界面产生的附加应力和界面间由于残留的低分子物而产生的界面的裂纹孔隙,在热冲击条件下(即放入高温的焊锡中),就会产生更大的集中应力,破坏界面间化学键或机械嵌合,使界面的粘接强度很快下降,而界面间残留的低分子挥发气体不断体积增大,活动能量也不断得到补充和加强。这时,已遭到破坏的界面上的粘接力抵抗不住这些挥发气体通过界面上裂纹、孔隙向外散发的内部破坏的力,就会在薄弱的界面上发生铜箔和基板,或基板层间的局部分层、起泡。
纸基覆铜板在热冲击条件下,出现“起泡”问题,是界面遭受到严重破坏的结果。根据板的类型,树脂配方,制造工艺条件不同,界面结构的破坏形式略有差异。在做耐浸焊实验中,其“起泡”的形状、分布瞬时发生的变化也是不同的。当用的树脂分子量分布或固化交联较均匀,树脂较纯清时,其板内界面应该是均匀的,试样放入焊锡中维持不起泡的时间是较为一致,起泡一般出现个别的大泡,起泡瞬间伴有响声,爆发力大。树脂中含有少量杂质时,测浸焊时会出现个别大的泡。杂质破坏了连续的界面层,并甚至可把上胶纸层面垫起一个深深的凹处,在它的周围空隙中易聚积较多的气体和应力,造成界面较大的缺陷,测定数据分散性较大。增强材料含有较大的杂质(如不溶的化学纤维块,较大较硬的纸浆块等)也会出现这种破坏界面层现象。若在测浸焊过程中试样铜箔在同一瞬间普遍出现均匀分布,直径差异不大的泡,一般是界面存有低分子(挥发物)太多。或者是树脂普遍固化交联不好,层间粘接力差的原因。这样化学键在高温条件下没有什么抵抗其破坏应力的能力,界面结构很快被严重破坏了。在测浸焊中,若试样在边缘有一排小泡出现,可能是由于板的半成品或成品吸潮,界面孔隙中进入水份引起的。进入的水分子不但扩大了孔隙的空间,而且在热冲击条件下,产生水蒸汽使界面上的孔隙发生倾向于增大、扩展的变化。有的试样放入较小的焊锡槽测定时,出现焊锡温度突然下降2—3℃的情况,可能是该板界面的裂纹、孔隙较多,受热后迅速扩展应力,吸收活动能量而造成的。一般这种板其耐浸焊性偏低且不稳定。研究上述板在热冲击下界面遭到严重破坏即“起泡” 的不同特点,对于我们分析、找出诸破坏因素的主要因素,调整或改变生产工艺条件,以及新产品板的树脂配方的设计都是有很大的帮助和启发。
(三)提高和稳定耐浸焊性的一些措施
提高和稳定纸基覆铜板的耐浸焊性,就要尽量消除和减少在板的成型和高温下会破坏各界面结构的诸因素。在制造覆铜板过程中,应注意以下各点:
1.铜箔要有稳定的较好的粗化处理层。
2.铜箔胶粘剂要有一定的耐热性和高粘合性。有时两者在胶粘剂配方选择、研制中是相互矛盾的,但两者都要达到一定高的程度。
3.树脂在固化交联时要均匀性好,缩合水产生的少,低分子挥发物少。并应有较高的交联密度,为此采用两种或两种以上的复合催化剂为宜,且树脂制造工艺应严格控制,在树脂制造过程中,尤其在热加工脱水时一定不要将胶液抽到冷凝器中,使冷凝器堵塞。如果冷凝器堵塞或部分堵塞,脱水时间非常长,这时上层水很难脱出,进而造成胶包水,水包胶,如果用这种树脂去上胶压板,不仅影响耐浸焊性,同时覆铜板也会产生严重翘曲。如何解决这个问题?办法1,树脂操作时操作者一定精心操作,不可有丝毫麻痹,而将胶液抽到冷凝器中;办法2,在反应釜蒸发器上安装一个“阻胶器”或在回流装置上安装一个缓冲罐;办法3,经常检查冷凝器,看一看是否有胶液堵塞现象,如遇有堵塞现象,及时疏通清理干净。若采用两次上胶工艺,其一次上胶纸挥发物要尽量控制低。二次必须是疏水性的。
4.树脂中的助剂(主要是阻燃剂、增塑剂、固化促进剂等),要选择挥发性小,耐热性高的。阻燃剂中反应型优于添加型,可选择合适的偶联剂加入树脂中,以提高耐热性或提高湿态粘合性。
5.要考虑树脂和铜箔胶粘剂固化时间(胶化时间),反应交联的匹配。有两侧加上胶玻纤布的纸基覆铜板 ,还应注意两种树脂的胶化时间和交联结构的匹配。
6.上胶纸挥发物的大小,对板的耐浸焊性有很大的影响。要保证上胶纸有较低的挥发物指标,但同时也不能一味压低挥发物,而把可溶性(或流动度)控制得太小,影响界面的粘合性。上胶烘箱温度设计,要有较适宜不同树脂特点的温度层次。同时要注意上胶纸浸渍、干燥的均匀性,并防止残留杂物。
7.保证上胶纸的贮存条件(一般温度应在20--25℃,相对湿度在35%以下为宜),减少贮存期。含有一定极性基团的酚醛树脂的上胶纸在贮存期间的吸收空气中的水分子(吸潮),直观表现在其上胶纸挥发物的增大,对板的耐浸焊性会造成很大的威胁。
8.树脂制造、上胶纸的生产以及压制工序中配料、叠合过程中都要防止杂质的混入。生产现场环境的净化清洁,对产品内在质量也至关重要。
9.压制过程中的压力、温度要合适。压制温度过高,会破坏界面的化学键,造成热分解反应。压制温度低、压力小,会造成固化交联不好,它们都会影响板的耐浸焊性。压制时还要注意压机热板中部和周边的温度应基本保持一致。在夏季潮湿气候条件下,配好的料坯,不及时压制,也会造成料边缘吸潮,影响耐浸焊性。
10.两侧加上胶玻纤布的纸基覆铜板,在浸焊性有一定独特的性质:此类板的脱蜡玻纤布与纸纤维之间的树脂界面,主要是通过“点、格”状形式粘接交联的,这种样式比起纯纸板的“片、层”状粘接附着力是偏弱的。其二,脱蜡布易吸潮。玻纤布的浸透性不如纸纤维。其三,上胶玻纤布和上胶纸一般为两种配方树脂,要达到树脂整个界面的均匀一致是有限的。由于上述原因,此类板在制成成品后,在潮湿条件下,板的耐浸焊性下降幅度大。因此一方面要注意包装防潮,又要注意将此类板耐浸焊性的实测值要做出高于指标的几倍,以有“保险余量”。
二、剥离强度
(一)剥离强度的测定
剥离强度是覆铜箔板中一个重要的质量指标,也是一项常规检验项目。它是覆铜板生产中常出现的质量问题。剥离强度低就会在印制版加工时或装机焊接时出现铜箔脱落问题,甚至会影响整个电器的正常运行。按照国家标准,剥离强度测定方法,要模拟印制电路板在加工工艺过程中可能经受的各种严酷条件,测定铜箔与基材间宽度的粘合力。这些模拟条件包括:①干热后(经500小时);②暴露于三氯乙烷蒸气处理后;③热冲击后(5秒/260℃);④模拟电镀条件暴露后;⑤在溶剂中浸泡后(浸没溶剂10分钟);⑥高温下做剥离强度试验。
(二)对提高胶接强度的认识
胶接强度,一般由两大部分决定:其一是粘合力。也就是铜箔胶粘剂和基材树脂通过在压制中受压受热,产生熔溶——交联的作用力,及上述两种树脂的混合物与增强材料之间作用力。其二,铜箔与增强材料树脂的内聚强度。这里指的树脂虽然包括上胶过程中浸入的增强材料的主树脂,也包括铜箔所涂胶粘剂,但关键是铜箔的胶粘剂。
达到粘接很强的必要条件,是铜箔胶粘剂对铜箔粗化面的很好的湿润。这种湿润不但是在铜箔涂胶工序中均匀的涂胶,还有在压制初期通过高压高温来实现。由于胶粘剂在靠铜箔一侧能很好的湿润、渗透到铜箔粗化面凹凸的表面层中,又在靠基材的一侧与主树脂很好的进行化学交联,才能保证较高的覆铜板的剥离强度。前者的联接,是固化之后是形成象许多小钩子似的状态,把胶粘剂和被粘物(铜箔)连接在一起。有人把这种形成的粘附力归于机械作用,这种胶接理论为机械力结合理论。按这种理论,较高的表面能和高比表面积对胶接强度有利。
(三)抗剥力的破坏
从覆铜板的铜箔胶接结构的断面上看,是由基板层(树脂和纤维增强材料的复合材料)、铜箔胶粘剂与树脂的界面层、铜箔胶粘剂层,铜箔处理的粗化层,铜箔基本层五层结构组成的。它们的彼此的力学性能是相差很大的。例如:铜箔及其粗化处理层是刚性弹性体,而胶粘剂则是弹性体。因此,胶接接头在承受外力作用时应力分布是非常复杂的。由于各个材料的热膨胀系数、固化收缩率不同,以及要受到水、溶剂、热氧化等环境介质的影响,都会生成胶接各层内和之间的应力,而且内应力的分布不均匀的。加之胶接结构的内部缺陷。在做剥离强度试验中,抗剥力的破坏总是会发生的,只不过有抗剥力高、低之分。这种抗剥力的破坏有四种形式:①胶粘剂与树脂界面的破坏;②铜箔胶粘剂的内聚力破坏;③铜箔粗化处理层破坏;④混合破坏。
(四)保证抗剥强度稳定性的主要措施
保证剥离强度稳定性包含有两个含义:一方面,要达到剥离强度在标准规定的各项指标。另一方面,剥离强度在覆铜板的各部位应均匀一致。
达到上述要求,包括两方面保证条件:较好的胶粘剂(耐热性强;胶粘强度高;并且有一定内聚强度;具有好的湿润能力;抗化学药品性好;耐潮性好;贮存稳定性好;与树脂很好的匹配等)。另一方面,在板的加工生产中工艺技术得到保证。其中应注意:
1.电解粗化铜箔的粗化质量稳定、均匀、无划伤、磨损。
2.树脂要有一定的交联密度,与铜箔胶粘剂应匹配。
3.树脂中的助剂(包括增塑剂、阻燃剂等),对胶粘剂与树脂的固化交联无削弱、破坏作用。
4.铜箔涂胶,纸的上胶其含量不能太小,可溶性、流动度不能太小,并且含量、可溶性均匀,保证半成品的贮存期。半成品的材料防止着水。
5.压制的预温、热压保温阶段要在时间、温度、压力方面达到工艺要求。
6.铜箔胶粘剂要达到工艺要求。
三、翘曲度
(一)翘曲度指标的重要性及测定方法
覆铜板翘曲度,板的翘曲通常指弓曲和扭曲两种变形。所谓弓曲是覆铜板的四个角都在同一个平面内,其边沿两条直线边在同一平面内。所谓扭曲是覆铜板的三个角座落在同一平面内,而另一角悬起成翘曲。在研究板的翘曲问题时,又可把它分为静态翘曲和动态翘曲,一些标准均只规定了静态翘曲的测定方法。
IEC标准推荐平台测定法。欧、美和世界不少国家均采用此法。我国国家标准也采用此法。其测试方法简述如下:将覆铜板凹面向上,置于长、宽不小于460mm的平台上。使直尺下边轻轻接触试样两端翘起的边缘,从主尺上读出跨距L(mm),并测量板与主尺上表面的最大距离h,用h减去主尺厚度,即板的弓曲值D。按下式换算成1000mm跨距时的弓曲值d,
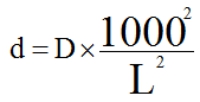
由于国标中翘曲度指标d较大,此项指标失去实际意义。一般还要尊重用户的意见,达到更小的翘曲度。另一种测定方法是日本JIS悬挂测量法。
单面覆铜板的弓曲值,铜箔在向上,且板呈凸形为正翘曲。反之,为负翘曲。
覆铜板的翘曲对于板使用质量影响极大。在印制板加工过程中,若翘曲度大,就会影响加工流水线的定位孔的精度,会因翘曲在丝网漏印中把网拽破,甚至翘曲过大,还不能通过流水线。在冲孔加工中也会带来麻烦。在整机组装过程中,由于印制电路板翘曲大,会影响计算机控制的元器件的自动插装;会影响过波峰焊时和元器件腿焊后自动“砍头”时的质量。甚至由于翘曲度很大,会造成过波峰焊时“塌腰”严重,焊锡流入非铜箔面,使整个带元器件的印制电路板的报废。
(二)覆铜板翘曲的原因
1.静态翘曲与动态翘曲
静态翘曲是指生产出的覆铜板的本身翘曲。动态翘曲是指覆铜板在加工印制电路板过程中,受热、受潮、受水影响以及在整机装配时通过波峰焊接过程中,受瞬时热冲击影响造成的翘曲。要创造出高质量、高水平的板,就要达到这种翘曲都小。从研究和解决两大翘曲出发还可以将这两大翘曲,分为以下几种情况(其中“+”表示一般为正翘曲,“—”表示为负翘曲)。
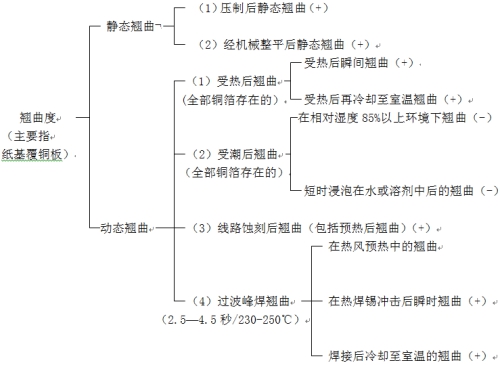
静态翘曲是与增强材料、树脂配方以及板在制造各工艺过程中情况有关,静态翘曲尽量要小,因为这对于动态翘曲的减少有很大的好处,因此,对纸基覆铜箔板,生产后进行一次整平加工是十分必要的。
可以看出,一种覆铜板的动态翘曲包括四种不同的翘曲,而且翘曲方向不同。覆铜板从出厂到印制板加工后,中间经过多道工序。主要是板面清洁及干燥;涂抗蚀剂及干燥;蚀刻及清洗抗蚀剂;涂阻焊剂及干燥;印字符(正反面)及干燥;预热和冲孔,涂助焊剂及干燥等工艺过程。在这些过程中,由于板受冷、热和溶液、溶剂的冲洗、浸泡等外界因素的影响,产生伸缩率不同,应力各异的内部结构变化,造成板的各类翘曲。将印制板加工后进入整机生产过程,先是装插元器件,然后投入自动焊接(波峰焊)。在这个过程中板的翘曲度也在变化。上述各种加工过程印制板的翘曲方向并非向某一方向增大的。而是板在不同加工过程向不同方向增大(或缩小)。动态翘曲的最理想的状态是在印制板制成后和波峰焊结束后,板的翘曲度接近零。
2.翘曲产生的原因
覆铜板的翘曲原因是一个十分复杂的问题。总体来讲,有以下几方面:
(1)覆铜板是由铜箔、树脂、增强材料(有的板具有两种不同增强材料)组成的复合材料。它们的热传导、热膨胀系数、化学收缩率相差很大,在固化成型、受热、受潮的不同条件下,产生内应力,造成翘曲。
(2)单面覆铜板是一种非对称结构的材料,更引起内部存在的应力含水率不均匀造成异向性变形。
(3)在纸板中,增强材料的纵、横膨胀、收缩率不同,使板的横向翘曲大于纵向翘曲。
(三)减少覆铜箔板翘曲应注意的问题
由于覆铜板翘曲问题比较复杂(特别是纯纸基板),影响因素是许多方面的。它包括增强材料、主树脂配方,树脂助剂,树脂的制造,半成品浸渍干燥、压制,后期处理以及产品的贮存包装等。归纳有以下主要几方面:
1.铜箔方面:a、伸长率大小b、铜箔的厚度c、上胶铜箔的含胶量及胶粘剂配方。
2.增强材料(主要指纸纤维):a、纸浆类型;b、纸纤维和纤维素含量;c、纸浆成份比;d、抄纸方式(长网或圆网);e、纸的幅宽厚度均匀程度;f、纸的吸水高度及均匀一致性;g、纸的抗张强度纵向与横向差;h、纸的热收缩、浸水后膨胀的纵横差异;i、纸的水分含量(10)纸的浸水膨胀,受热收缩的情况。
3.树脂:a、树脂的配方;b、树脂的增韧性(增塑性);c、树脂的固化交联特性;d、树脂的粘度与浸透性;e、二次树脂的疏水性;f、助剂的影响(包括阻燃性、增塑剂、固化剂、固化促进剂等);g、树脂制造中的均匀性。
4.半成品的浸渍、干燥工艺:a、浸渍的程度、均匀性b、挥发物、树脂含量的影响。
5.压制工艺:a、压机热板温度的一致性;b、压制升温与冷却的速度;c、配料的配置、搭配;d、各种半成品材料、钢板的纵、横方向的一致性;e、压制时热板内通热气的方向与板坯方向的一致; f、压制的温度、时间、压力;g、卸板温度;h、垫纸的厚度和使用次数;i、压制中流胶情况。
6.板的后期处理:a、包装;b、储存条件;c、整平质量。
上述几方面的因素,要根据板的类型,树脂的配方结构,生产条件找出关键的主要因素,加以解决。同时,要认识到翘曲问题总是多种因素交叉在一起构成的。有时也需要“综合治理”。
四、表面干花
板的表面形成局部或大面积的麻面,称为表面干花。这种现象往往在薄板中易于出现。
(一)产生原因
1.上胶半成品的含胶量偏低,流动度(或可溶性)偏小,因而在压制时树脂的流动性差,不能很均匀的在层压板表面成膜。
2.压制时受热不均匀,由于压机热板的边缘特别是四角向周围空气的传热速率大,压机预热时热板中央部位(芯部)和四角部位有时相差大,故坯料边角的树脂流动性差,若预热时压力跟不紧,形成边角干花,若加热的热板内汽路不畅,则局部温度过低,形成条状及片状干花。
3.压制时预热时间过长,而且压力偏低。在树脂反应大部分进入B、C阶段之前未能及时跟紧压力。
4.压制时受压不均匀,由于热板和托板(即鱼头板)多次磨擦,使托板与加热板不免存在缺陷,使局部压力偏低,形成干花。
5.由于冷却不充分,卸板后钢板温度过高,又立即叠合下一模板,而且未能及时压制,由于坯料在较高温度下存留时间较长,在不受压的情况下绶慢进行反应,加之预热时压力偏低,也会造成表面干花。
(二)解决方法
1.备料、配料时要特别注意上胶半成品的流动度(或可溶性),不能偏低。一般的层压板的上胶半成品均分为本体和表面两种,即俗称的里、面。在配薄板时,要选择树脂流动性好的表面纸,要注意上胶半成品的贮存期不可过长,夏季不得在较高温度下贮存。
2.方案搭配时,要考虑薄板性能与相应的厚板搭配一起生产,以增加坯料的弹性和传热受压的缓冲,使受热、受压均匀。
3.由于产品性能要求或产品规格的限制,薄板单独压制时,垫纸就要厚一些,且要经常更换。
4.压制时预热时间不可过长,要视流胶情况、压力要跟紧,这样不仅对减少表面干花且对层压板的其它性能的提高也有帮助。
5.不锈钢板经常研磨,四个角首先易偏薄。这样,在压制时四个角受呀偏低,也易出现干花,边角花。如果检测不锈钢板四角偏薄过大,就要更换了,不可继续使用。
五、板表面粘住钢板
这种现象在环氧玻纤布板中较为常见,即层压板脱模不好。板的表面树脂部分附着在表面上,造成层压板的表面胶膜被破坏,严重者对钢板的表面质量也有损坏,影响生产的顺利进行。
(一)产生原因
1.板压制期间树脂固化不完全,由于压制温度低或压制时间短,使树脂固化不完全尚残留一部分可反应的基因。如环氧基羟基等。这些极性反应基团氧上的未共用电子对可进入金属(不锈钢板)元素中的空轨道,使之与钢板间的表面亲合力大于树脂分子间力,使树脂的脱模能力大大降低,造成粘钢板。
2.胶液在贮罐内存放时间过长,树脂的内脱模剂在胶液中分散不均匀,造成局部脱模剂量少。
3.外来的极性基团,主要为空气中的水份。夏季由于空气湿度大,若压制冷却时通水时间过长,钢板温度过低。钢板表面会凝结极细微的水滴;上胶半成品从空调间推入压制车间也会在上胶玻纤布表面有冷凝水;操作者的汗水;清除垫纸时的水都会落在钢板上;树脂中某些原料含水分过多等,水是极性分子,有利于树脂与钢板间的粘合,故夏季粘钢板现象要比其它季节严重。
4.同一套钢板连续多次压制环氧玻纤布板后,钢板表面树脂的残留量越来越多。对某些需涂外脱模剂才能有利的层压板生产的,当外脱模剂涂擦不均,也会引起粘钢板。
(二)解决方法
1.保证热压时间及压制温度。经常在压制保温阶段放蒸汽,以排出加热板管路中的冷凝水,保证压制温度。夏季如担心可能会粘板时,可先拉出一层,观察压制固化程度,遇有粘板发生,可适当延长热压时间。
2.夏季下板温度不宜过低,若发现钢板过凉时,可适当通蒸汽回热,然后再下板。若下板后,钢板较热,可用风机吹风降温,然后再叠合,以免因钢板过热导致表面干花。
3.如发现钢板上有水及其它杂质要及时擦去,并涂擦适量的外脱模剂。
六、坯料滑出
坯料和钢板在压制预热、升温及热压前期沿层向滑出,俗称“跑板”,这种现象以环氧玻纤布板居多。
(一)产生原因
1.预热时间过短,预热温度过高,压力过高,打压过于频繁。
2.坯料受热不均匀,坯料两边的温差较大。坯料两边的树脂不是同时熔化、流动,造成一边比另一边先熔化。形成坯料受压不均匀,或对于跑板造成压机柱塞受到径向阻力,导致压机的压力不均匀,在后面几模板压制预热时也易跑板。
3.坯料的树脂含量偏高,流动度偏大或上胶半成品两边的流动度差别较大;或同一炉坯料中有一部分坯料流动度偏大。
4.树脂中脱模剂量过多。
5.压制规格搭配不合理。如边缘薄板的规格偏厚。预温不易热透。
(二)解决方法
1.配板时正、反倒料,使其含胶量、流动度尽量均匀。
2.推板前将加热板温度升至预温温度,使其加热板各部位温度基本均匀,然后将坯料推入压机压制。
3.根据半成品的树脂含量、流动度及存放时间的长短,选择适宜的预热压力,控制加压次数,且要密切观察流胶情况。
4.根据层间总厚度的不同,灵活掌握预温时间,充分热透,避免在层中间坯料温度较低的情况下,急速升温、加压。
5.密切观察,如发现“跑板”迹象,立即采取措施。如在预热阶段树脂未胶化前,可快速通水,将坯料冷却后拉出重新叠合、压制。或不拉出,适当降低压力和温度,并用木块等物塞顶住,防止进一步滑出,待稳定后再开启蒸汽和加压,继续压制。
6.压制易“跑板”的板,不要频繁自动补压(指预热期间)。
七、层压板厚度偏差大
由于设备的精度所限,同一块层压板的厚度也不均匀,因此厚度单点偏差是绝对的,但也有其它原因。
(一)产生原因
1.板的中央厚,边缘薄,这是因压制时板边缘流胶较多所致。
2.板的一边偏厚,一边偏薄,这主要是上胶半成品流动度一边偏大,一边偏小或热板的一边温度高,一边温度低以及热板倾斜所造成的。
3.由于市场需求,用户对板的厚度偏差范围要求越来越小,造成部分层压板超差。
(二)解决方法
1.配料时倒料。使其流动度尽量均匀一致。
2.上胶半成品的上胶测定指标值及尺寸一致。
3.压制推板前先开启蒸汽阀门,将热板预热,压制过程中要经常放蒸汽,排出管路内及加热板中的积水,以防热板进汽一侧温度高,排放汽侧温度低。
4.预热时密切注视流胶情况,防止流胶过多。
八、其它
此外,尚有板表面的一些质量问题。如:板中间颜色深,四周颜色浅,同一模板,有的板颜色深些,有的板浅些,一般叫“色差”。表面积胶;表面压裂;表面树脂渣等问题。板中间颜色深,四周颜色浅,这种情况俗称“镜框”。产生这种情况的主要原因是上胶纸中挥发物比较大。在预热时四周挥发物易跑出,中间挥发物残留量大。因此四周颜色浅,中间深。应当防止上胶纸受潮。特别是上胶纸可溶性过大,相应的热压时产生的低分子物也多,此种现象也更为严重。试验证明低分子物比水份影响大,应尽量减少上胶半成品的挥发物。预温时压力小一些,时间长一些。
板的表面积胶是由于增强材料,本身厚度偏差较大,引起胶量不均或上胶机的缺欠造成胶纸某一位置胶量过大,当树脂流动性比较差,压力跟的不及时或偏小时,造成的表面积胶现象。因此,胶纸树脂含量要均匀,底材厚度偏差不能太大,压制时,注意压力要及时,不能过晚。
板的表面压裂主要是树脂在流动时打压过急,将底材压坏。其次,是增强材料强度太低所产生的。因此应当控制上胶半成品的流动度(可溶性),严格控制胶纸在流胶时打压次数和压力在预温开始不久一段,不能过高。对木浆纸强度过低的要拒绝使用。
板面的树脂渣是由于卸板时及叠合时,对钢板清理不干净,钢板上附着树脂渣造成的。因此将钢板及坯料清理干净再叠合。对不锈钢板的清理打磨要经常进行,这是保证覆铜板外观质量的关键环节。
综上所述,纸基覆铜板目前生产制造企业是量大面广,要认清形势,WTO入世在即,是机遇又是挑战;当前尤为重要的是要加强内部管理,下功夫练好内功。人们说,纸基板生产制造是三分技术,七分管理不是没有道理的。以工艺为突破口,达到两提高(提高质量,提高产量)一降低(降低以原材料为主的各种消耗)追求利润最大化。把量大面广的纸基板做好做大。同时要加强对PCB企业及整机电子企业下游客户的服务。将那些经过专业培训,既懂得覆铜板制造工艺,又懂得PCB工艺及整机电子加工工艺的优秀人员派到市场第一线,为客户服好务,这是覆铜板制造企业应有的义务和责任。同时,也是覆铜板制造业立于不败之地的可靠有力的保证。
|
|
|
|
|
|
|
热点新闻 |
|
|
|