第一节 概述
在电子整机产品中,覆铜板起着元件负载和电路互连、电路间绝缘三大作用。按所用基材的不同,覆铜板主要有纸基覆铜板、玻纤布覆铜板、复合基覆铜板、挠性覆铜板等几大类。由于玻纤布覆铜板具有强度高、耐热性好、介电性能好,基板通孔可以镀金属(俗称孔金属化),实现双面或多层印制板层与层之间电路导通。所以,环氧玻纤布覆铜板是覆铜板所有品种中用途最广,用量最大的一类,它广泛应用于通讯、移动通讯、电脑、仪器仪表、数字电视、数控音响、卫星、雷达等产品上。全世界各类覆铜板生产中,纸基覆铜板和环氧玻纤布覆铜板约占92%,环氧玻纤布覆铜板产量以面积计略大于纸基覆铜板,以重量或产值计则大大超过纸基覆铜板。纸基覆铜板大部分用于家用电器产品。当前,欧美地区已经很少生产和使用纸基覆铜板,亚洲地区对纸基覆铜板的生产量和使用量仍比较大。但随着电子产品向轻、薄、短、小,向数字化方向发展,印制电路板向精细图形,向高密度、高多层方向发展。原来使用纸基覆铜板的电子产品,逐步改用玻纤布覆铜板,使纸基覆铜板发展滞缓,玻纤布覆铜板特别是多层PCB用途玻纤布覆铜板得到更为迅速的发展。
覆铜板主要由铜箔、基材、粘合剂三大部分构成。覆铜板较常用的粘合剂有酚醛树脂、环氧树脂、改性环氧树脂、聚酰亚胺树脂、氰酸酯树脂、PPO树脂、BT树脂等。由于以环氧树脂制造的覆铜板具有成本较低廉、生产工艺性好,产品介电性能、机械加工性能优良,而被广泛用于单面,双面及一般多层印制电路板上。以环氧树脂或改性环氧树脂为粘合剂制作的玻纤布覆铜板是当前覆铜板中产量最大,使用最多的一类。在NEMA标准(美国电器制造商协会标准)中,环氧玻纤布覆铜板有四个型号:G-10(不阻燃)、FR-4(阻燃)、G-11(保留热强度,不阻燃)、FR-5(保留热强度,阻燃)。自对电器产品实施安全防火要求以后,进入美国电器产品须经美国安全保险实验室进行安全认证(简称UL认证)。在覆铜板产品中,非阻燃产品的用量在逐步减少。在环氧玻纤布覆铜板中,百分之九十以上的产品为FR-4型。当前FR-4型产品已发展为一大类可适用于不同用途的环氧玻纤布覆铜板的总称。在IP-4101C标准中已经命名的,属于FR-4型覆铜板产品有:24号产品,其树脂体系的主体为改性或不改性环氧树脂,阻燃,Tg150~200℃;25号产品,树脂体系为环氧/PPO树脂,阻燃,Tg150~200℃;26号产品,树脂体系为环氧树脂(用于加成法工艺),阻燃等。(IP-4101C还有很多FR-4型号的覆铜板)
国外好些覆铜板生产厂也都将FR-4形成一个系列化产品,以适应多种性能要求PCB制作用途,这种做法,值得国内各覆铜板厂家借鉴。
在FR-4型产品中,还有一种不是覆铜板,但销售量却非常大的产品——半固化片。半固化片用于多层印制板制作时把各内层板粘结起来,也是一种性能要求很高的产品。
不同型号环氧玻纤布覆铜板的生产工艺流程基本相同,他们主要区别是树脂配方不同。所以,在下面各节论述中,将以FR-4作为代表。由于当前覆铜板市场竞争十分激烈,各覆铜板厂对自己的工艺技术都有所保留。尽管如此,笔者在撰写本章时,力求将问题论述清楚。如果论述中有因涉及技术诀窍而说得不够明瞭的地方,希望读者能予以谅解。
环氧玻纤布覆铜板生产工艺流程,一般是分段式生产,它主要由四段构成:第一段为树脂配制;第二段为基材上胶;第三段为叠合(国外称叠书)与层压;第四段为修边与检验,包装。生产工艺流程见图7-1-1。

第二节 环氧玻纤布覆铜板树脂的组成与配制
树脂配方选用及树脂技术,是覆铜板生产工艺技术的最重要部分。所有覆铜板产品性能改进、覆铜板新产品开发,工作的核心是树脂配方的研究及树脂改性等,其次才是与新配方相适应的生产工艺技术。
当前,可以生产环氧玻纤布覆铜板的树脂配方很多,在G-10,FR-4,G-11,FR-5四个产品中,比较典型的树脂配方如表7-2-1所示。
表7-2-1 典型的树脂配方
材料名称 |
配比 |
G-10 |
FR-4 |
G-11 |
FR-5 |
双酚 A 型环氧树脂 |
100 |
|
100 |
60 |
四溴双酚A型环氧树脂(溴含量18~22%) |
|
100 |
|
|
高溴环氧树脂(溴含量 40 ~ 48% ) |
|
|
|
40 |
双氰胺 |
3 ~ 4 |
2.7 ~ 3.5 |
|
|
二甲基二苯砜 |
|
|
20 |
25 |
苄基二甲胺 |
0.2 ~ 0.4 |
0.2 ~ 0.4 |
|
|
2- 甲基咪唑 |
|
0.05 ~ 0.12 |
|
|
三氟化硼单乙胺 |
|
|
1.5 |
1.5 |
二甲基甲酰胺 |
15 |
15 15 |
15 |
15 |
甲基溶纤剂 |
15 |
15 15 |
15 |
15 |
丙酮 |
适量 |
适量 适量 |
适量 |
适量 |
从表7-2-1上看,各组分配比在较大变化范围内选用都可以作出覆铜板,但在同一型号产品中,采用不同材料,或采用相同材料而采用不同用量、不同配比,对覆铜板生产工艺性能及产品特性是有不同的影响,其中以树脂、固化剂和促进剂三者的材料选用及配比对产品的性能影响最大。
制造环氧树脂玻纤布覆铜板的原材料在第五章中已有论述,本节就环氧树脂玻纤布覆铜板可以选用的环氧树脂、固化剂、促进剂及其性能,树脂装置与调胶技术等,结合工艺配方及配制技术等作进一步论述。
一、环氧玻纤布覆铜板用环氧树脂
环氧玻纤布覆铜板主体树脂是环氧树脂,在一个型号产品中,它可以只采用一种环氧树脂,也可以采用两种或两种以上环氧树脂,或者用其它树脂(如双马来酰亚胺树脂、PPO树脂、氰酸酯树脂等)对环氧树脂进行改性,来改进提高覆铜板某一个方面的性能。本文重点介绍环氧树脂。
环氧树脂是分子式中含有2个或2个以上环氧基 的一类高分子化合物。由于环氧树脂分子结构中含有环氧基、羟基,使其有很强的反应活性和粘合性;环氧树脂固化过程是加成聚合,固化物没有水和其他低分子物产生,固化物收缩率较小,固化物具有较高的机械强度、优良的耐化学药品性能、介电性能,所以环氧树脂被广泛用于覆铜板生产。在覆铜板生产中较常用的环氧树脂有如下数种:
(一)双酚A型环氧树脂
双酚A型环氧树脂是由双酚A和环氧氯丙烷反应而成,它不是一种纯粹化合物,而是一种不同分子量聚合物的混合物,是一类用途很广泛的树脂,其化学结构式为:

分子结构中的双酚A骨架赋予机械性和耐热性,羟基、醚键、环氧基赋予高粘合力,醚链赋予耐化学药品性,亚甲基赋予柔顺性等,当分子结构中亚甲基数量越多,分子链越长时,其柔顺性越好。根据不同反应条件,可以得到n=0―20的不同分子量环氧树脂,n值从零到接近1的低分子量环氧树脂是液态的,n等于1或者大于1时的环氧树脂是一种脆性热塑性固体。在G-10型产品树脂配方中,当只用单一种环氧树脂时,常用环氧当量在450~550环氧树脂(相当于我国E-20型环氧树脂)。而当树脂配方中并用两种或两种以上树脂时,则常以E-20型树脂作为主体树脂,并入部分低分子量双酚A型环氧树脂如E-44或E-51,提高体系交联密度,以提高固化物的耐热性和耐化学药品性等。也有并入部分线性酚醛型环氧树脂(酚醛环氧树脂)F-44或F—51。由于线性酚醛型环氧树脂分子结构中含有较多环氧基,因而可以获得耐热性更加优良产品。我国G-10型覆铜板多数都在E-20中并入部分E-44,也有同时并入E-44及E-51,来达到预定产品目标(见表7-2-2)。
表7-2-2 树脂配方
材料名称 |
配比 |
Ⅰ |
Ⅱ |
Ⅲ |
E-20 型环氧树脂 |
80 |
80 |
80 |
E-44 型环氧树脂 |
|
20 |
10 |
E-51 型环氧树脂 |
|
|
10 |
双氰胺 |
4 |
4 |
4 |
苄基二甲胺 |
0.2 |
0.2 |
0.2 |
二甲基甲酰胺 |
15 |
15 |
15 |
乙二醇甲醚 |
15 |
15 |
15 |
丙酮 |
适量 |
适量 |
适量 |
在选用配方时,千万要防止片面追求提高某一性能,而忽略产品综合性能。在覆铜板生产中,单独追求某一性能很容易达到,但要达到优良的综合性能就很难了。它需要做树脂配方筛选及各生产工艺条件探索,PCB加工工艺性考察等。如体系中加入部分低分子量环氧树脂,提高了体系的交联密度,提高了产品耐热性和耐化学药品性。但体系固化收缩率也加大,内应力加大,增加产品翘曲度,此种情况在新产品研制中会经常遇到。因而改进、提高产品某一方面性能时,应同时注意产品其它方面性能,产品生产工艺性能及产品在PCB制程中工艺性等,衡量其得失,再作出取舍。
环氧树脂制品的性能与所选固化剂种类、固化剂的使用量及固化工艺条件密切相关,在覆铜板制造中,还与环氧树脂分子量及分子量分布范围相关,如环氧玻纤布覆铜板所采用的双酚A型环氧树脂分子量分布范围,就与覆铜板生产工艺性能密切相关。如胶液粘度、B阶时树脂熔融粘度变化范围等,就与基材上胶,覆铜板热压工艺条件设定密切相关。如FR-4型覆铜板所用双酚A型溴化环氧树脂,其分子量分布范围有所谓“单峰型”和“双峰型”(指红外光谱图形状)。单峰型表现为分子量分布比较集中,在产品热压成型时凝胶转变过程比较短,转变点比较明显。而双峰型表现为分子量分布范围较宽,产品在热压成型时凝胶转变过程时间较长,转变点没有单峰型那么明显,可操作时间较长。九十年代以前多采用单峰型环氧树脂,认为对提高制品性能有好处。但随着生产技术水平提高,环氧树脂中各种杂质成分,特别是有机氯,无机氯等含量降低,提高了制品介电性能及与固化剂反应性,而转向采用双峰型环氧树脂,以提高环氧玻纤布覆铜板制程中工艺性。在使用时应予以特别注意。而固化剂的用量又与环氧树脂的环氧值或环氧当量相关。
由于在拟定树脂配方,选用环氧树脂时要用到环氧值或环氧当量。在计算固化剂用量时又要用到环氧值或环氧当量,所以在此处对这二个问题的概念仍加以介绍。
环氧当量:含有1g当量环氧基的环氧树脂的质量克数。
环氧值:100g环氧树脂中环氧基的克当量数。
环氧当量 = 环氧树脂分子量/环氧基数
环氧值 = 100/环氧当量
(二)线性酚醛型环氧树脂
线性酚醛型环氧树脂有苯酚型酚醛环氧树脂和邻甲酚型酚醛环氧树脂两种类型,其化学结构式分别为:
苯酚型酚醛环氧树脂

邻甲酚型酚醛环氧树脂

线性酚醛环氧树脂中由于分子结构中含有较多环氧基及芳香核,固化产物交联密度很高,产品的耐热性,耐化学药品性更加优良。但由于此类树脂固化后产物较脆,树脂的粘合性也较双酚A型环氧树脂差,因而在覆铜板行业中不单独使用,以免覆铜板铜箔剥离强度太低和基板分层,而是与其它树脂并用。如在G-10型覆铜板中,并入部分线性酚醛环氧树脂,以提高基材耐热性和耐化学药品性(见表7-2-3)。
表7-2-3 树脂配方
材料名称 |
配比 |
Ⅰ |
Ⅱ |
E-20 型环氧树脂 |
80 |
85 |
酚醛环氧树脂 |
20 |
|
酚醛环氧树脂 |
|
15 |
双氰胺 |
4 |
4 |
苄基二甲胺 |
0.2 |
0.2 |
二甲基甲酰胺 |
15 |
15 |
甲基溶纤剂 |
15 |
15 |
丙酮 |
适量 |
适量 |
由于线性酚醛环氧树脂加入量过大时会影响产品综合性能,对于只要求适度提高产品耐热性能产品,加入量一般不超过25%。
在G-11及FR-5型产品中,也常用到线性酚醛环氧树脂,典型树脂配方将在固化剂及其他相关部分论述。
(三)阻燃剂与溴化环氧树脂
随着电子元器件功率加大,整机组装密度提高,导致电子装置失火事故增加。为了防止火灾发生,各种电子元器件,包括覆铜板必须符合安全防火要求,它促使阻燃型覆铜板的诞生和迅速发展。组成环氧树脂玻纤布覆铜板三大材料中,铜箔和玻纤布是不会燃烧的,要制造阻燃型覆铜板,就必须在树脂系统中加入阻燃性材料。在元素周期表中第VA族的N、P、As、Sb、Bi,第Ⅶ族中的F、Cl、Br、I以及Al、B、Zn、Sn、Ti、Mo等元素本身或化合物,都具有一定阻燃性能。阻燃剂总的分为添加型(也称非反应型)阻燃剂和反应型阻燃剂两大类。
添加型阻燃剂是指具有阻燃性能的有机物或无机物,但这类阻燃剂,是分散在树脂体系中,不参予树脂体系固化反应。较常用的卤素类有机化合物,如氯化石蜡、十溴二苯醚、五溴二苯醚等,卤素类无机物如溴化铝,砱系类有机物如砱酸三苯酯、砱酸三甲苯酯等,砱系无机物如砱酸铝;其他化合物,如Sb2O3,Al(OH3等等。但在实际生产中,很少单一使用一种阻燃剂,而是两种或两种以上并用,对于一些阻燃剂,并用后由于有协同阻燃作用,只要加少量就可达到比只加单一种阻燃效果大得多的作用。如卤素化合物与三氧化二锑共用有协同作用;砱和氮,砱和卤素共用有协同作用等。添加型阻燃剂在纸基覆铜板中用得较多,在环氧玻纤布覆铜板中用得较少,主要是使用后基板透明度下降及耐热冲击性下降。
反应型阻燃剂是指参予树脂固化反应的物质,当前用得比较多的是溴化环氧树脂及含阻燃元素固化剂(在谈到环保型覆铜板时再论述)。由于卤素类是阻燃功能较强的一类元素,在卤系元素中,阻燃性能依次为I > Br > Cl > F ,但以溴化物用得最多。溴化环氧树脂主要有溴含量为48~50%的高溴化环氧树脂;溴含量为19~21%的低溴化环氧树脂和溴化线性酚醛环氧树脂。它们的化学结构式分别为:
高溴化环氧树脂化学结构式

低溴化环氧树脂化学结构式

溴化酚醛环氧树脂化学结构式

FR-4型环氧玻纤布覆铜板常用低溴环氧树脂,而在FR-5型覆铜板中,为了提高产品耐热性需加入部分多环氧基或芳核含量较高树脂,而需采用高溴环氧树脂,以保证产品耐燃性能达UL94-VO级。典型树脂配方见表7-2-4。
表7-2-4 树脂配方
材 料 名 称 |
配比 |
FR-4 |
FR-5 |
低溴环氧树脂(溴含量 18 ~ 22% ) |
100 |
|
高溴环氧树脂(溴含量 48 ~ 50% ) |
|
75 |
酚醛诺伏腊克环氧树脂 |
|
25 |
双氰胺 |
4 |
|
2- 甲基咪唑 |
0.1 |
|
二氨基二苯砜 |
|
15 |
三氟化硼单乙胺 |
|
0.8 |
二甲基甲酰胺 |
15 |
|
乙二醇甲醚 |
15 |
|
甲乙酮 |
|
60 |
(四)双酚S型环氧树脂
双酚S型环氧树脂化学结构如下:

其分子结构与双酚A型十分相似,但由于分子结构中含有砜基,所以制品耐热性明显优于双酚A型环氧树脂。此类树脂可用于提高覆铜板耐热性时的改性用途。
(五)多官能基环氧树脂
在覆铜板行业较常用的多官能基环氧树脂主要有:
四苯基缩水甘油醚基乙烷,其化学结构式为:

三苯基缩水甘油醚基甲烷,其化学结构式为:

这一类型环氧树脂由于具有高芳核含量和多环氧基,固化产物交联密度高,使制品具有优良耐热性,在FR-4型覆铜板中,常通过并入部分多官能环氧树脂来提高基板Tg。当前,在FR-4产品系列中的阻UV光基板,就是通过添加部分四苯基缩水甘油醚基乙烷来实现的,在后面阻UV光覆铜板中再行详细论述。
二、固化剂和固化促进剂
环氧树脂是一种用途非常广泛的高分子化合物,但它必须在加入固化剂固化了以后才能实现其使用价值。环氧树脂固化是通过其活性基团——环氧基开环来实现交联固化的,它是加成反应,固化过程不产出水和小分子化合物,因而其在热固化过程不会像某些缩聚型树脂(如酚醛树脂)其固化产物易产生气泡和较大收缩率,因而在覆铜板制程中,环氧树脂体系制品热压固化成型压力可以比酚醛树脂体系制品小得多。
可使环氧树脂固化的固化剂品种相当多,凡是具有两个或两个以上活泼氢的化合物都可以作为环氧树脂固化剂。主要有胺类、酸酐类和树脂类。下面主要介绍在覆铜板生产或产品试制中用到的一些固化剂。
(一)胺类固化剂
胺类固化剂是环氧树脂固化剂中用得最多的一类固化剂。在覆铜板行业中用得较多的为改性多元胺及潜伏性固化剂。下面分类叙述之:
1.脂肪族多元胺
脂肪族多元胺类固化环氧树脂的反应历程为:
伯胺中的活泼氢先使环氧树脂开环反应,生成仲胺:

仲胺中活泼氢再和环氧树脂中环氧基发生开环反应:

反应持续进行,形成网状交联体系。
反应生成的羟基,在有催化剂存在的场合下也能使环氧基发生开环反应:

日常所见的乙二胺,二乙烯三胺等脂肪族多元胺等固化剂属室温固化剂,固化物收缩率较大,不适宜于覆铜板生产用途。在覆铜板生产中多用改性多元胺固化剂,如:
590固化剂是二乙烯三胺与环氧丙烷苯基醚加成物,其结构式为:

593固化剂是二乙烯三胺与环氧丙烷丁基醚反应物,其结构式为:

594固化剂是胺基硼烷型化合物,其结构式为:
胺值80-130
595固化剂也是胺基硼烷型化合物,其结构式为:
胺值200-300
这些改性多元胺固化剂具有如下优点:
(1)和环氧树脂混溶性很好;
(2)和环氧树脂以一定比例混溶后,在最初1~2个小时内粘度有所增加,但此后粘度可保持3~4个月没有多大变化;
(3)由于其碳链较长,因而固化产物韧性较好。固化过程中及固化后产物受热时均没有小分子物产生,因此产品热态下电性能好;
(4)和环氧树脂混溶后,在常温下反应较慢,但在120℃以上,2~3个小时就可固化,固化时放热量不大,易控制。
由于这类固化剂具有上述优点,我国有些覆铜板厂在环氧玻纤布覆铜板生产中,将其与双氰胺作为并用固化剂,旨在弥补以双氰胺为固化剂,覆铜板产品所存在耐热性、耐潮性不足等缺陷。树脂配方见表7-2-5。
表7-2-5 树脂配方
材 料 |
配 比 |
E-20 型环氧树脂 |
90 |
E-44 型环氧树脂 |
10 |
双氰胺 |
3.5 |
594 固化剂 |
1.5 |
苄基二甲胺 |
0.3 |
二甲基甲酰胺 |
15 |
乙二醇甲醚 |
15 |
丙酮 |
适量 |
根据上述配方生产的覆铜板的耐浸焊性,耐湿热性都较仅以双氰胺为固化剂制品有一定提高。
2.芳香族胺类
芳香族胺类固化剂由于分子结构中含有芳香核,固化后产物的耐热性和耐化学药品性优良,适于有较高耐热性要求产品,在覆铜板生产中较多采用的芳香族胺类固化剂有:二氨基二苯甲烷(DDM)、4.4一二氨基二苯砜(DDS)等。其与环氧树脂固化反应历程与脂肪族胺类固化反应历程相同。这一类型固化剂常被用作耐热性玻纤布覆铜板的固化剂,如常被用在G-11及FR-5型覆铜板中。(参见表7-2-1)。
3.潜伏性固化剂
覆铜板生产过程是分工序的、间断过程。它有胶液配制工序,粘结片生产工序及热压成型工序。当工序与工序之间衔接不是很紧凑时,每道工序制品就产生储存,这就要求配制好的胶液或已生产出来的粘结片在室温下不会发生固化反应,有一定储存时间。特别是作为商品用途的半固化片,用户收货后不可能一次用完,它要求半固化片应在数个月时间内保持其技术参数在符合使用要求范围内。这就需要一种在常温下不与环氧树脂发生固化反应,而在升高到一定温度下能快速固化环氧树脂的固化剂。这类固化剂被称作“潜伏性固化剂”。在覆铜板生产中,双氰胺是最常用的潜伏性固化剂。双氰胺,虽然存在吸潮性大,只能溶解在强极性溶剂中,跟铜接触会发生反应生成“胺铜”盐类,降低铜箔与基板结合力等缺陷,但由于双氰胺材料来源广泛,价格便宜,潜伏性固化剂特性很突出,以其为固化剂制取覆铜板,产品性能及覆铜板工艺性、PCB工艺性均较优良,所以至今环氧玻纤布覆铜板仍以其为固化剂。
双氰胺英文全称Dicyandiamide(简称Dicy),结构式为:

分子式为:C2H4N4
分子量:84.08,为白色棱形结晶颗粒(或粉末),不可燃,熔点207~209℃。溶解于强极性溶剂如二甲基甲酰胺,乙二醇甲(乙)醚及水中,不溶于丙酮,苯等非极性溶剂,与环氧树脂相溶性很差。为了防止双氰胺溶解不良析出,覆铜板用双氰胺应磨成细小颗粒或粉末。
从分子式上看,双氰胺分子中有一个“一级胺”—NH2,一个“二级胺”=NH,一个“三级胺” ,是一个反应性很强,固化机理比较复杂的化合物。
通常,以胺类作为环氧树脂固化剂,其用量按下式计算:
胺类固化剂用量(%) =环氧值× 胺分子量/胺中活泼氢原子数
=胺当量×100/环氧当量
双氰胺胺当量 = 84.08/4 ≈21
当前,G-10及FR-4型覆铜板所用环氧树脂的环氧当量,制造厂家不同时,虽然牌号相同,但其环氧当量仍有较大差别,如有的厂家这一型号环氧树脂环氧当量在410~460(平均值435),而有的厂家则为450~510(平均值480)。
如果按环氧当量435计算:
双氰胺用量(%)= 21/435×100=4.83%
如果按环氧当量480计算:
双氰胺用量(%)= 21/480×100=4.38%
上述计算方法,实际上是按当量反应定律即环氧当量与胺当量等当量反应为依据。即不管用那种环氧当量计算,在G-10及FR-4型覆铜板中,按上式计算,每100份环氧树脂中应加入固化剂双氰胺用量均超过4份。但在实际生产中,双氰胺的加入量为环氧树脂加入量的3~3.3%时,产品的Tg值就已很高,说明在该配比下,产品已充分固化。即实际生产中双氰胺用量较按双氰胺分子中活泼氢原子数计算量要少得多。这说明双氰胺除了四个活泼氢参加反应之外,分子中的氰基(—CN)在高温下也参予了与羟基或环氧基反应。因此,在覆铜板生产中双氰胺实际用量少于按双氰胺活泼氢数计算的理论用量。关于双氰胺中的氰基(—CN)参予固化环氧树脂反应历程可能是:
(1)双氰胺N上的四个活泼氢和环氧树脂的环氧基反应,生成N—羟基氰基胍:
(Ⅰ)
然后(Ⅰ)式中的羟基(—OH)再和氰基(—CN)发生反应形成网状交联结构:
(Ⅱ)
(2)双氰胺本身先分解为氨基氰(其中部分生成三聚氰胺,三聚氰胺部分溶解于环氧树脂中,部分继续分解为氨基氰)。氨基氰的两个活泼氢再和环氧树脂中的环氧基进行反应,生成的含有羟基、氨基直链低聚体再进一步反应形成网状结构:
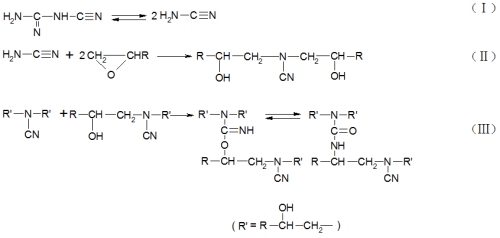
(3)高温下,双氰胺N上的四个活泼氢先和环氧树脂的环氧基发生开环反应,生成N—烃基氰基胍[见(1)-Ⅰ]。在此过程中,双氰胺有部分离解成三聚氰胺及氨基氰[见(2)-Ⅰ]。其后反应可能有(1)-Ⅱ,(2)-Ⅱ,(2)-Ⅲ。
(4)在没有促进剂存在场合,双氰胺需在160℃以上才开始发生活泼氢对环氧基的开环反应,生成N—烃基氰基胍。在有促进剂存在场合,则反应温度下移。从DSC曲线上看,在以二甲基咪唑为促进剂的溴化环氧树脂/双氰胺体系中,在60℃时已有反应产生,但反应很缓慢,到120℃附近,反应开始加剧,曲线逐步变陡,150~160℃为固化反应高峰,到170~180℃固化反应基本结束,(见图7-2-1)。
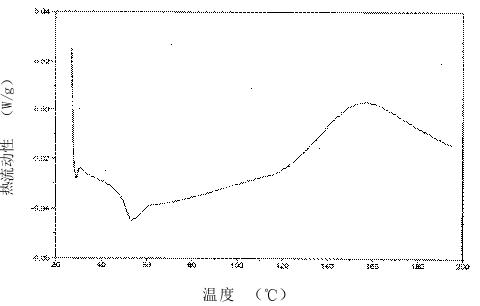
图7-2-1 双氰胺固化环氧树脂动力学曲线
在有促进剂存在及反应温度低于140℃时,双氰胺与环氧树脂反应主要发生在伯氨基上的单取代加成反应,而且反应速率较慢;当温度高于140℃时,则双氰胺的仲氨基可进行双取代加成反应,而且它的氰基也可以与开环后羟基或环氧基发生如下反应:
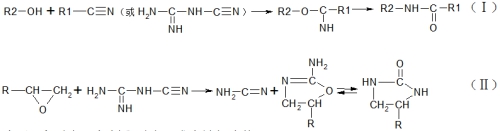
(R1、R2表示双氰胺与环氧树脂反应形成直链低聚体)
由上可见,双氰胺固化机理相当复杂,它既不只是双氰胺上的四个活泼氢参予反应,氰基也参予反应,即应有五个反应基。但有人对固化体系的交联密度进行实测及计算,又认为实测交联密度比按五个反应基计算交联密度小。上述情形,使双氰胺固化剂用量难以准确计算,也就形成了当前同一个FR-4型覆铜板实际生产树脂配方中,双氰胺的用量高的有用到3.5份,低的有接近2.5份的情况出现,而在配比差别如此大情形下,各厂生产出来的FR-4型产品均各获市场认定。这说明决定FR-4型覆铜板质量问题不仅与双氰胺相关,也与其它材料用量及工艺条件相关。其关键是在设定树脂配方中双氰胺用量及促进剂(如2-甲基咪唑)用量时,要对胶液凝胶化时间(GT)设定及粘结片树脂含量(RC%)、粘结片凝胶化时间(GT)、粘结片流动度(RF%)及生产工艺条件进行综合平衡处理,才能达到设定树脂配方时的预定目标。
4.有机酰肼
有机酰肼,分子式为H2N—NH—CO—R—CO—NH—NH2,在常温下不与环氧树脂起固化反应,只有加热后才跟环氧树脂产生固化反应,也是一种潜伏性固化剂,其固化物耐水性、对金属粘合性优于双氰胺固化体系,而且这类固化剂分子链较长,有利于提高分子链柔顺性,降低产品翘曲度,但未见广泛推广应用报导。
(二)酸酐固化剂
酸酐固化剂是一种在加热条件下才能与环氧树脂发生固化反应的一类固化剂,酸酐固化环氧树脂,制品的介电性能比胺类固化更加优良。因此,国内外均有覆铜板生产厂将其作为环氧玻纤布覆铜板的固化剂。较常用的有邻苯二甲酸酐,六氯邻苯二甲酸酐、甲基四氢邻苯二甲酸酐、甲基六氯邻苯二甲酸酐、甲基迪纳克酸酐、二苯醚四酸酐等。
酸酐对环氧树脂固化历程为:
(1)在无促进剂时:
环氧树脂中的羟基使酸酐开环成单酯。
(Ⅰ)
羧基再和环氧基发生加成反应成二酯:
(Ⅱ)
在酸存在条件下,环氧树脂中的羟基与环氧基发生醚化反应:

(2)在有促进剂时(如以叔胺为促进剂)
叔胺与酸酐形成离子对:
(Ⅰ)
羧基负离子打开环氧基,生成酯键,同时生成新的阴离子:
(Ⅱ)
新的阴离子又促使酸酐开环或促使环氧基开环,进一步发生醚化反应:
(Ⅱ)
这是阴离子开环聚合反应至体系形成网状结构。
酸酐类固化剂用量可用下式计算:
每100g环氧树脂所需酸酐量=K×(酸酐分子量/酸酐分子中酸酐基因数) ×环氧值
式中的K值根据酸酐的活性,经由实验确定的系数,通常K值小于1(通常取0.6~0.8,在以叔胺作为促进剂场合,K值可以取1)。
由于不同种类酸酐固化剂,不同种类固化促进剂对环氧树脂固化反应历程及固化反应速度有很大差别,所以在实际生产中应根据价格,工艺性能及产品要求去衡量、选择。
酸酐固化剂在环氧玻纤布覆铜板应用实例见表7-2-6。
表7-2-6 树脂配方
原材料名称 |
配比 |
E-20 型环氧树脂
邻苯二甲酸酐
甲乙酮 |
100
40
适量 |
(三)高分子类固化剂
可以作为环氧树脂固化剂的高分子物很多,如线性酚醛树脂、聚酯树脂、橡胶类树脂等。其中以酚醛树脂用得比较多,其它类型树脂通常作为改性成分,如为了提高基板耐热性或增韧目的才加入。
1.酚醛树脂
酚醛树脂分子上含有大量的酚羟基和羟甲基,在加热条件下可以使环氧树脂中环氧基开环交联形成网状结构。这种固化物既保持了环氧树脂良好的粘合性、介电性,又具有酚醛树脂的耐热性。通常双酚A型环氧树脂固化物长期使用温度不超过200℃,但以酚醛树脂固化环氧树脂固化物长期使用温度可以达260℃。用酚醛树脂作为环氧树脂固化剂在绝缘材料行业用得很普遍。我国早期生产的环氧玻纤布覆铜板,就有一类是以酚醛树脂作为固化剂,典型树脂配方如表7-2-7。
表7-2-7 树脂配
原材料名称 |
配比 |
E-44 环氧树脂
酚醛树脂
丙酮
酒精 |
60
40
适量
适量 |
这类覆铜板具有价格低廉,耐热性好等优点,但透明度不如纯环氧树脂,不方便PCB进行线路检查,因而未能获得进一步发展。但以酚醛树脂固化环氧树脂路子,会继续被应用。
以酸为催化剂制得的酚醛树脂为热塑性酚醛树脂(也称诺伏腊克或线性酚醛树脂)。其结构为 ,以碱为催化剂的酚醛树脂为热固性酚醛树脂(也称雷琐尔酚醛树脂),在覆铜板生产中主要用可溶于丙酮及酒精的A阶树脂,它是羟甲基酚与低缩聚物的混合物,为低缩合树脂,其可能含有如下各个成分:

热塑酚醛树脂与环氧树脂固化反应,需有促进剂(如苄基二甲胺)存在下,酚羟基使环氧基开环聚合:
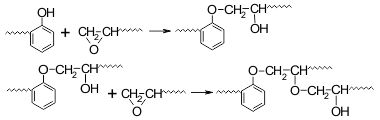
在热态下热固性酚醛树脂与环氧树脂进行固化反应,酚醛树脂的酚羟基和羟甲基均能使环氧基开环聚合。同时,酚醛树脂本身也能交联聚合而形成一个体形结构:
酚羟基使环氧基开环起醚化反应:
(Ⅰ)
酚醛树脂中的羟甲基与环氧树脂中羟基反应:
(Ⅱ)
酚醛树脂中的羟甲基使环氧基开环起醚化反应:
(Ⅲ)
再有酚醛树脂本身自交联而形成体形结构。
随着电子产品高密度组装而对基板提出越来越高的耐热性要求,以双氰胺为固化剂的环氧玻纤布覆铜板已不能满足这一要求。由于酚醛树脂分子中含有较多芳香核而使体系具有较高耐热性,而且由于酚羟基邻对位具有很高活性,可以引入各种基团或元素进行改性,合成具有预定性能的新材料,如环保型覆铜板要求无卤成分,较适宜阻燃剂为N或P,将N或P引入到酚醛树脂中并以其作为环氧树脂固化剂,可以作为生产该产品的一种方法。也有人试验用双酚A与甲醛反应制取双酚A型线性酚醛树脂,用其来作为环氧树脂固化剂,制品的Tg及热失重温度较以酚醛树脂固化环氧树脂产物还有所提高,并且解决了以酚醛树脂/环氧树脂体系产品透明度较差的问题。
2.聚硫橡胶
聚硫橡胶是环氧树脂优良增韧改性剂,其改性原理为聚硫橡胶末端的硫醇基(-SH)与环氧树脂的环氧基发生开环反应,从而使固化体系含有柔性链段,提高了环氧树脂固化体系的柔韧性。在覆铜板生产中,增韧目的是为了消除产品内应力,提高产品平整性。作为传统的环氧树脂增韧橡胶弹性体尚有端羧基丁腈橡胶等。由于橡胶弹性体的加入会降低固化体系的耐热性和机械性能,因此,选用时要慎重。
(四)固化促进剂
在覆铜板生产中,为使胶液和粘结片有较长储存期,选用固化剂都是常温下不反应,高温下才起固化交联反应类型。为了使固化温度及固化时间能在预先设定的范围内,这就需要加入能适当降低固化温度,适当缩短固化时间的化合物,以适合生产工艺的要求,这类化合物被称作固化促进剂。在环氧玻纤布覆铜板生产中常用固化促进剂有如下数种:
1.叔胺类
实际上叔胺类本身就是环氧树脂的固化剂,它对环氧树脂的固化历程为:
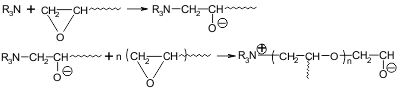
它是阴离子型加成聚合反应。但在以双氰胺为固化剂体系中,少量叔胺对调整环氧树脂/双氰胺体系的固化温度和固化时间有明显作用,所以在覆铜板行业叔胺常被当作固化促进剂使用,比较常用的有苄基二甲胺(BDMA)和2、4、5一三(二甲氨基甲基)苯酚(DMP-30)、三乙醇胺等。具体应用参见表7-2-1。
2.咪唑类
咪唑本身也是环氧树脂固化剂,它是具有两个氮原子的五元环,一个氮原子构成仲胺,一个氮原子构成叔胺。所以咪唑既有仲胺固化作用,又有叔胺的催化作用。
咪唑与环氧树脂的固化机理为:
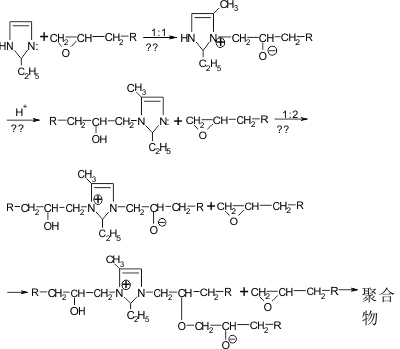
咪唑类可以直接作为环氧树脂的固化剂,其固化物具有优良的耐热性。由于在以双氰胺的固化剂的体系中,少量咪唑对降低环氧树脂/双氰胺体系的固化温度和缩短其固化时间有明显作用,所以也常被当作固化促进剂使用。比较常用的有2-甲基咪唑(2-MZ)、2-乙基-4-甲基咪唑(2E4MZ)、2-苯基咪唑(2PZ)、2苯基4甲基咪唑(2P4MZ)。
3.三氟化硼单乙胺(BF3-400)
BF3是一种路易士酸,它是环氧树脂的阴离子聚合型催化剂,其催化聚合机理如下:
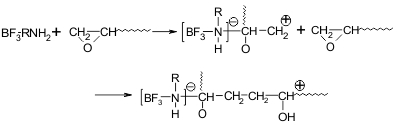
但在覆铜板行业中很少将其单独作为固化剂使用,更多的是将其当固化促进剂使用,如在G-11及FR-5型覆铜板中(参见表7-2-1)。
三、溶剂
环氧玻纤布覆铜板生产中常用溶剂有丙酮、甲乙酮、乙醇、二甲基甲酰胺、乙二醇甲醚、甲苯等。这些溶剂的主要物性如下:
丙酮:英文名acetone。分子式C3H6O,结构式CH3COCH3。是最简单的饱和酮。无色易挥发易燃液体,相对密度(d 20 4 )0.7848。熔点―94.6℃。沸点56.1℃。闪点(开杯)―16℃。其蒸气与空气形成爆炸性混合物,爆炸局限2.15%~13.0%(体积)。自燃点538℃。丙酮微带香气,有轻度毒性,对眼、上呼吸道有刺激作用。不宜过多吸入丙酮蒸气,操作场所应通风。
丁酮:别名甲乙酮。英文名butanone。分子式C4H6O,结构式CH3CH2COCH3。无色易燃液体,有丙酮气味。相对密度(d 20 4 )0.8054。沸点79.6℃。熔点―85.9℃。闪点(开杯) ―6℃。在空气中的爆炸局限1.97%~10.1%(体积)。自燃点515.6℃。
甲乙酮有中度毒性,长期吸入甲乙酮蒸气会使眼、鼻、喉等粘膜受刺激而引起炎症。操作场所应保持良好的通风,操作人员应戴口罩和橡胶手套。当皮肤或眼睛接触到甲乙酮后,应立即用大量清水冲洗。
乙醇:别名酒精。英文名ethanol。分子式C2H6O,结构式CH3CH2OH。无色透明,易挥发易燃液体。溶于水。无水乙醇相对密度(d 20 4 )0.7893。熔点―117.3℃。沸点78.32℃。闪点(开杯)14℃。工业乙醇(含乙醇95%)相对密度(d 20 4 )0.816。沸点78.15℃。自燃点793℃。
N,N-二甲基甲酰胺:英文名N,N-dimethylformamide;DMF。分子式C3H7NO,结构式HCON(CH3)2。无色透明液体,为强极性溶剂,溶于水。相对密度(d 20 4 )0.9445。熔点―61℃。沸点152.8℃。闪点58℃。自燃点445℃。
二甲基甲酰毒性较低,对皮肤和粘膜有轻微刺激。
乙二醇甲醚:别名甲基溶纤剂。英文名ethylene glycol monomethylether。分子式C3H8O2,结构式HOCH2CH2OCH3。无色透明液体,具有令人愉快的气味。相对密度(d 20 4 )0.9647。熔点―85.1℃。沸点(102.391kpa)125℃。闪点46.1℃。自燃点288.3℃。
有毒性,能引起贫血症,操作场所应有良好通风,操作人员应穿戴劳动护品。
甲苯:英文名toluene。分子式C7H8,结构式 —CH3。无色透明液体,可燃。相对密度(d 20 4 )0.8667。熔点―95℃。沸点110.6℃。闪点4.44℃。自燃点536.1℃。在空气中爆炸局限为1.27%~7.0%。
具有中等毒性,对皮肤及粘膜有刺激性,对神经系统有毒性。操作场所应有良好通风,操作者要穿戴劳动护品。
在选用溶剂时,既要考虑其溶解能力大小,又要考虑其沸点高低。通常,不能单独使用低沸点溶剂,以免在上胶过程,因溶剂挥发过快而造成树脂体系粘度不稳定,影响粘结片树脂含量均匀性,或粘结片进入烘箱时,因溶剂挥发过快,由于表层先挥发变干而内层尚未挥发,而造成“外焦里嫩”、气孔等现象产生,而得不到品质均一优良制品。此外,溶剂挥发太快有可能导致双氰胺结晶析出,严重影响制品质量。因而,应高、中、低沸点并用,形成沸点梯度的溶剂组合,以免因胶液中溶剂挥发太快,而造成胶液粘度变化过大。在烘箱中,让溶剂分段逐步挥发,避免粘结片产生气孔、粘结片表面有“火山口状”、或“外焦里嫩”现象发生。特别是以双氰胺为固化剂时,由于双氰胺跟环氧树脂不相溶,又只能溶解于强极性溶剂中,溶剂的选取及用量确定,既与生产成本相关,也与防止双氰胺析出,保证产品质量相关。在环氧玻纤布覆铜板树脂配方中,较常用的双氰胺溶剂有二甲基甲酰胺(沸点是153℃);也有采用二甲基甲酰胺和乙二醇甲醚(沸点是124.6℃)并用。二甲基甲酰胺及乙二醇甲醚对双氰胺的溶解性都较好,加入乙二醇甲醚以后可以形成更有层次的溶剂沸点梯度。也有在溶剂体系中加入甲乙酮(沸点79.6℃),甲乙酮只能作为环氧树脂溶剂,加入甲乙酮的主要目的也是为了使溶剂沸点梯度层次更加合理。
双氰胺是一种吸湿性很强的化合物,有不少文章论述水对以双氰胺为固化剂的制品性能产生危害,这与双氰胺在环氧树脂体系中较易析出及双氰胺吸潮性较强有关。实际上,水也是一种溶剂,是一种对双氰胺有良好溶解性的极性溶剂,国内外就有一些覆铜板厂将水与DMF并用作为双氰胺溶剂,用于环氧玻纤布覆铜板生产,产品的性能也相当优异,在此提供给各位同行。(见表7-2-8)。
表7-2-8 树脂配方
原材料名称 |
配 比 |
E-20 型环氧树脂 |
100 |
双氰胺 |
4 |
二甲基甲酰胺 |
14 |
蒸馏水 |
3 |
丙酮 |
适量 |
四、树脂溶液的配制
对于以双氰胺为固化剂的环氧树脂溶液,由于双氰胺不溶于一般有机溶剂,所以应该单独溶解,然后再与环氧树脂溶液混合。由于双氰胺溶解性与温度有关,在45℃时双氰胺在强极性溶剂中很容易溶解,如果气温较低,双氰胺不易溶解时,可适当加热使其溶解完全。促进剂应加在双氰胺溶液中,再与环氧树脂混和,不要加在双氰胺与环氧树脂混和后的溶液中。因为促进剂的用量很少,加在混和后的溶液中,不易分散,不易混和得很均匀,会影响产品性能一致性。
对于其它类型固化剂使用,也尽量采用这一原则,以提高固化剂及促进剂在胶液中分布均匀性。
固化剂和树脂经过充分溶解和充分搅拌混和均匀后,应当让胶液熟化若干小时,让各组分有足够相互接触,相互渗透与反应时间,使体系到达一个稳定平衡状态。对于以双氰胺为固化剂,以苄基二甲胺为促进剂的树脂体系,从胶液GT值变化,要达到稳定平衡状态最少要16小时,以2-甲基咪唑为促进剂的树脂体系,熟化时间为6~8小时。固化剂和促进剂加入环氧树脂以后,体系存在反应,分子量在发生变化,因此胶液熟化是必要的。随着存放时间延长,胶液GT会逐渐缩短,因此,胶液有一定贮存期限制。
配制好的胶液停放时间过长时,特别对于溴化环氧树脂胶液,自上至下会产生一个浓度梯度,使用前应当开动搅拌,使其恢复均一状态后再投入使用。
五、树脂溶液调配装置
树脂溶液调配装置设置合理性与否跟生产成本产品质量有关系,所以将其作为一个专题加以论述。
(一)原材料贮罐
覆铜板生产中用到大量供应商用丙酮或甲乙酮溶解好的环氧树脂溶液和大量有机溶剂。这些原材料供应有桶装的,也有散装的。使用桶装材料要增加包装费,要有较大库存面积,库存面积大火灾危险性也大。生产过程中桶装材料加料通常采用泵来抽,有些厂甚至采用直接倒,这种操作方式火灾危险性很大。而且,对于比较粘稠的环氧树脂溶液,有抽不干净或倒不干净现象存在。通常桶底残留量在1%~3%,如果操作者责任心不强,其残留量还会更大,这都是增加成本的因素。因此,对于环氧树脂溶液及有机溶剂,有条件时,应尽量采用贮罐贮存。
采用罐装材料有如下优点:
1.产品质量方面
罐装材料可以用管道输送,计量加料。可以实现自动化控制,避免了桶装加料人为计量差错,因而可提高产品质量。
2.产品质量一致性方面
覆铜板产品质量一致性是用户要求,是覆铜板厂技术水平、管理水平具体反映。影响产品质量一致性因素很多,有原材料质量分散性影响、设备因素影响、生产工艺波动影响等。在原材料方面,不同厂商提供的不同批次原材料质量不尽相同。就是同一厂商所提供的不同批次原材料质量也有差异。因此,有不少覆铜板厂采用贮罐来贮存和混不同批次原材料,以减少和消除不同批次原材料间质量差异(对于不同厂商同一型号原材料,通常不混用。如要混用,应当经过试验,确认对产品质量不会造成影响以后才可混用。),以给覆铜板生产提供质量更趋一致的原材料。
3.生产成本方面
包装材料减少,库存用地减少,加料损失减少,加料速度加快,相应使生产成本降低。
4.安全生产方面
覆铜板产品中虽然大部分属于阻燃型(如FR-1、FR-2、FR-4、FR-5等),这些产品离开火源后自己会熄灭,但在有火源时仍会继续燃烧,而且这些产品所用的大部分化工原材料,有机溶剂都是易燃易爆物品,其中大部分属于火灾甲类危险品(如丙酮、甲醇、乙醇、甲苯等)。安全生产,防止火灾事故的发生是每个覆铜板厂生产中时刻应当注意的事项。原材料采用罐装以后,库存面积减少了,生产过程为管道化密闭式生产,所以火灾危险性降低,生产安全性提高。
对于原材料贮罐材质,应尽量采用不锈钢。因为环氧玻纤布覆铜板产品质量要求较高,有些液态原材料对钢材虽然不产生腐蚀,但贮罐长期与大气相接触,罐体就会有铁锈产生,这些铁锈进入产品,就会影响基板外观及降低基板绝缘性能。
(二)调配装置
当前,环氧玻纤布覆铜板生产用环氧树脂都由供应商提供,并且已用丙酮、甲乙酮或甲苯等溶剂配成固体量60%~80%的树脂溶液,覆铜板厂生产时只要把树脂溶液与固化剂混合在一起即可。混胶罐的结构可以采用反应釜式,全密闭结构;也可以采用气动搅拌,半密闭结构(见图7-2-2)。双氰胺等固化剂需单独溶解,也可采用气动搅拌,半密闭结构(带夹套,以在天冷气温较低,双氰胺不好溶解时可往夹套中通入热水,促使双氰胺完全溶解)。树脂混配装置全部采用不锈钢制。如果采用反应釜式全密闭结构,罐的体积可以做得大一些(如5000L或更大),如果采用气动搅拌,半密闭结构,由于气动搅拌器功率限制,通常罐体体积以2000L~3000L为宜。
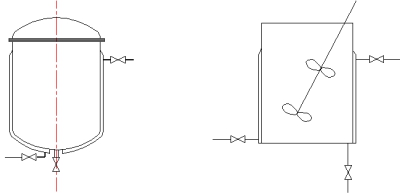
A、密闭式混胶罐 B、半密闭式混胶装置
图7-2-2 树脂溶液混胶罐
混胶罐数量配置,通常采用一个在配胶生产、一个在熟化、一个在供胶给上胶机使用原则。
搅拌器的形式,可以采用锚式、框式、桨式或螺旋推进式。螺旋推进式搅拌器是在转轴末端装有2~3片推进式螺旋桨(对于罐比较深的,也有装二排甚至三排螺旋桨)。螺旋桨叶一般都较小,转速较快。螺旋推进式搅拌器对物料造成湍动程度不高,但循环量大,它适用于低粘度溶液。但如果胶液中加有颗粒状填料时,固体颗粒会被抛向罐底,造成分相。因此,对于加有填料的胶液,不宜采用螺旋推进式搅拌器。
使用螺旋推进式搅拌器时,搅拌速度不能太快。因为这类搅拌器当搅拌速度很快时,液面中心部位会明显下陷甚至可露出桨叶中心部位,导致空气进入。
对于采用锚式,框式或桨式搅拌器,而且釜体体积又比较大时,搅拌器将很重。为了取得平稳的搅拌效果,通常在釜底中心部位作一球形支托来支撑搅拌器,支托应采用耐磨材料。由于出料口也设在釜底中心部位,所以设计支托时,应使其不会阻碍放料。
(三)物料计量
上面我们提到采用原材料贮罐及加大反应釜容量等措施,有利于提高产品质量一致性,加料准确性也是提高产品质量及质量一致性的重要一环。
对于管道输送物料,通常采用管道流量计进行计量,其精度应不低于千分之一至万分之五。也可以采用计量罐计量,其计量精度应也不低于万分之五。
计量罐加料过程是先在自动控制装置上设定加料重量以后,启动加料泵开始加料,当重量达到设定值时,泵自动停止,即加料停止。但此时管道中仍有物料,为了防止泵停止以后仍有物料进入计量罐,影响加料准确性。进料管道应设计成外斜形,以使泵停止时物料即倒流,管道中物料不会进入计量罐(见图7-2-3)。
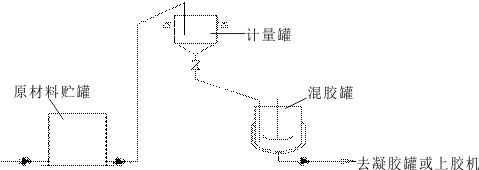
图7-2-3 计量罐称重加料示意图
当然,也可以采用将配胶罐放在计量精度为万分位的电子秤上,边加料边累加计量等等方法。但对于系统而言,采用流量计及计罐,系统的自动化程度更高一些。
(四)物料输送
覆铜板生产中,各种液体原材料及胶液输送可以采用齿轮泵,隔膜泵或离心泵等。离心泵结构简单,流量均匀,流量大,但输出压头不够高,适宜于低粘度液体输送。齿轮泵靠齿轮缝隙空间输送流体,流量小,但压头高,适宜于输送粘稠流体,如环氧树脂溶液。隔膜泵靠二片隔膜连续不断的胀开与挤压往复运动,将流体连续地吸入和排出而达到流体输送的目的。它适于高粘度流体及含填料流体输送,当流体含有大量易燃易爆溶剂时,采用气动隔膜泵安全性更好。采用气动隔膜泵时要认真计算工厂压缩空气供应量,以免因压缩空气供应灵不足而影响工厂动力供应。隔膜泵的膜片多数为橡胶类或聚四氟乙烯类,使用寿命约半年,使用时应备用隔膜以当隔膜有损坏时可及时更换,以免影响生产。
所有泵均应不锈钢制。
(五)树脂车间地点与安全防火
树脂车间地点应尽量靠近上胶机,以尽量缩短混胶罐(贮胶罐)到上胶机输送胶液管道长度。如果管道太长,特别是有些覆铜板厂建全厂树脂中心,和上胶机距离较远,输送胶液管道既长,而且暴露在室外,受风吹雨淋日晒,一旦停产数天或更长时间,管道里的胶液就需清理掉不能用,造成浪费。而且管道在室外受太阳暴晒,靠管壁部分温度可能较高,使靠近管壁的胶液有可能产生凝胶。胶液在管道中输送时,靠管壁部分受阻力较大,流速相应较慢,致使靠近管壁处产生凝胶机会加大。日积月累,管道有可能因有凝胶产生而逐步变窄到可能发生堵塞。因而树脂车间设置不宜远离上胶机,室外的胶液输送管道应包保温层。
由于覆铜板厂生产中大部分液态化工材料为有爆炸危险的甲、乙类物品,因此树脂车间一定要严格执行消防防火规定。输送丙酮、甲醇、乙醇等低沸点溶剂入料管道要接近罐底,以免加料过程因摩擦、冲击产生静电,引发火灾。国内有些溶剂厂发生特大火灾,检查事故发生原因,就是加料入料管离罐底太远,罐体又没防静电接地,在加料过程中因溶剂冲击罐体,产生静电而引发特大火灾,造成严重财产和人员生命损失,应引以为戒。树脂车间设备要有静电接地装置,接地电阻要符合消防防火要求。室内要有排气设施,以及时排走一旦发生溶剂洩露时充斥在室内的挥发物。车间内所有电器均需防爆,车间内要配备足够消防器材。
由于胶液粘度稳定性、一致性对粘结片(半固化片)各项技术指标有相当大影响,而胶液粘度稳定性、一致性除了和溶剂的种类及用量有很大关系外,与温度也成正比。即温度越高,胶液粘度越低。为要保证生产过程胶液粘度稳定、一致,对于北方寒冷地区,混胶罐、贮胶罐,浸胶槽等设备应有夹套,外包保温层,生产中往设备夹层通入一定温度热水以使系统恒温,对于南方地区覆铜板厂,也要达到生产稳定,产品质量一致,也应采用上述作法。要取得更高技术层次产品,对设备,对生产工艺技术条件就必需加严控制。
六、树脂技术
在这里我们讲的树脂技术指覆铜板产品性能改进或新产品开发,进行树脂配方的研究与筛选时,树脂并用嵌段,接枝,共聚合等对环氧树脂进行改性的技术及两种或两种以上固化剂并用技术或固化剂改性技术。
(一)并用环氧树脂及环氧树脂改性技术
覆铜板性能改进,新产品开发,其工作核心是树脂配方的研究,筛选,试验适应新树脂配方的生产工艺条件。传统的G-10和FR-4型环氧玻纤布覆铜板树脂配方中,是采用单一种环氧树脂。如G-10产品是采用环氧当量450~520双酚A型环氧树脂,FR-4型产品是采用环氧当量450~520溴含量19~21%溴化环氧树脂(见表7-2-9)。
表7-2-9 树脂配方
原 材 料 名 称 |
配方 |
G-10 |
FR-4 |
环氧当量 450 ~ 520 双酚 A 型环氧树脂 |
100 |
|
环氧当量 450 ~ 520 溴含量 19 ~ 21% 溴化环氧树脂 |
|
100 |
双氰胺 |
3-4 |
3-4 |
苄基二甲胺 |
0.2-0.4 |
|
2- 甲基咪唑 |
|
0.05-0.12 |
二甲基甲酰胺 |
15 |
15 |
乙二醇甲醚 |
15 |
15 |
丙酮 |
适量 |
适量 |
至今,有不少覆铜板厂G-10及FR-4型产品仍沿用上述配方进行覆铜板生产,它虽然被大量用于印制电路板制作,但难以满足高性能印制电路板制作要求。当今,日本各大覆铜板公司在FR-4型覆铜板上已不是单一个品种,而是一个产品系列,以适用于各种品质要求PCB制作。如果拿我们单一树脂体系的FR-4型覆铜板和日本相同型号产品作平行性能对比检测,我们会发现这种产品在介电性能,耐热性能等方面和日本产品会有一些差距。因此,覆铜板厂FR-4型覆铜板不能停留在单一环氧树脂,单一型号产品中,应进一步提高产品性能,拓宽产品系列化范围,才能满足技术水准日益提高的PCB板制作要求。
在环氧玻纤布覆铜板产品性能改进,新产品开发中,最简单和最有效的一种方法就是采用并用环氧树脂技术。二十世纪七十年代,我国在开发G-10型覆铜板时,初始的树脂配方就是表7-2-1中的树脂配方,虽然也生产了大量G-10型覆铜板投放市场,但产品综合性能与国外产品存在不少差距,特别是产品的耐热性,耐化学药品性不能令人感到很满意。在对该产品性能改进中,就是采用并用环氧树脂技术。如往原配方中添加部分低分子量双酚A型环氧树脂或添加部分线性酚醛环氧树脂(酚醛环氧树脂),提高了固化体系的交联密度或增加体系中耐热性,耐化学药品性好的芳香基含量,达到了提高产品耐热性,耐化学药品性目的,使产品的性能有了明显提高。但是,在树脂配方研究,筛选时,千万注意不能片面追求某一性能。如果只为提高产品的某一性能,是很容易做到的。但要达到在某一性能提高同时,产品全性能也满足PCB板制作要求,是有相当难度的。如在原树脂配方中加入低分子量双酚A型环氧树脂以后,它的固化收缩率大于高分子量双酚A型环氧树脂。固化收缩率加大,势必加大固化产物内应力,就会影响到产品平整度。树脂配方的筛选有如中医师开中药方一样,每味中药都有它自己的药性,如何选药及每味药用多大量对治病都会有不同效果。树脂配方筛选也同样存在选用什么树脂及各成分比例、用量,对产品性能都会有不同影响的,只有多方面进行平衡,才能去弊存利,开发出某一性能提高同时,综合性能也优良产品来。
当前,市面上已有很多的高性能环氧树脂销售,在改进提高FR-4型覆铜板性能时,应充分利用这些树脂。阻UV光的FR-4型覆铜板就是通过并用四官能基环氧树脂实现的,开发其它技术要求覆铜板也可以尝试走这一条路。在试制中,千万注意制品综合性能,制品覆铜板生产工艺性能及在PCB制程中的工艺性能要反复研究摸索,才能成功。
当采用并用树脂技术不能满足产品性能要求时,可以用某些高性能树脂对环氧树脂进行改性,如接枝,共聚合等方法,充分利用环氧树脂优良粘结性、反应性、覆铜板生产工艺性和PCB制作工艺性,再赋予它新性能。这也是高性能环氧玻纤布覆铜板新产品开发常用方法。
(二)并用固化剂与固化剂改性技术
当前,我国有不少覆铜板厂G-10及FR-4覆铜板生产仍为单一环氧树脂或单一固化剂树脂配方。它已不能适应日益发展的PCB制作要求,FR-4型覆铜板产品系列化、耐高热覆铜板、高频用途覆铜板、高尺寸稳定性覆铜板、高多层、精细线路覆铜板的开发与发展,都是覆铜板科技工作者的重要课题。因此,我们FR-4型覆铜板不能停留在单一品种状态中。应加强新产品开发力度,进一步提高产品性能,拓宽产品系列范围。在新产品开发中,并用环氧树脂是一种简单而有效的方法。同样,并用固化剂技术也是改进,提高产品性能的一种简单而有效方法。如当采用单一固化剂制得产品性能已不能满足更高性能印制板要求时,针对所要改进,提高产品性能要求,可以并用某一可以达到该要求的固化剂到现用的树脂配方中去,来提高产品的这一方面性能。如对于只用双氰胺作为固化剂的环氧玻纤布覆铜板,产品的耐热性,耐潮性不够理想。为了解决这一缺陷,国内有一些覆铜板厂在树脂配方中,将594型固化剂与双氰胺并用,制出产品的耐热冲击性能有了明显提高,耐潮性也有所提高。
也有一些覆铜板厂选用3,3'-二氯4,4'-二氨基二苯甲烷(MOCA),化学结构式为:
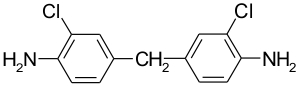
它是聚氨酯橡胶的硫化剂,但当把它与双氰胺并用作为环氧玻纤布覆铜板固化剂时,收到很好效果,产品的耐热冲击性及耐潮性都有不少提高。因而,在覆铜板性能改进,新产品开发时,可以考虑并用固化剂途径。可以与双氰胺并用的固化剂,除了一些环氧树脂常用固化剂之外,能与环氧树脂起固化反应的高分子类化合物,也可作为并用固化剂。使用前须先确定目的,如以提高覆铜板平整度为目的时,可在树脂配方中增加部分分子链较长,柔顺性较好的,具有反应活性的低分子或高分子类化合物,使固化体系形成一个“互贯穿网络”结构,制出覆铜板的平整度会有很大提高。
在采用并用固化剂技术进行新产品研制时,往往会同时使用并用环氧树脂技术。即在树脂配方中可以有两种或两种以上环氧树脂及两种或两种以上固化剂。但在应用时一定要综合考察制品全性能,包括PCB制程工艺性能。如在FR-5型覆铜板研制时,如果并用芳核含量较多环氧树脂、同时有并用芳核含量较多的固化剂时,虽然可以制得耐热性能很优良的覆铜板,但产品的硬度可能会偏高,在PCB制程中钻头的磨耗可能较大,排屑性可能会较差等,是必须防止的。
虽然双氰胺存在溶解性差,吸潮性较大,固化温度较高,固化产物耐热性不足等缺陷,但它具有常温不与环氧树脂反应,高温下才起固化反应,环氧树脂/双氰胺体系在覆铜板制程及PCB制程工艺性能良好等优点,而被选作环氧玻纤布覆铜板的主要固化剂。如何克服双氰胺缺陷而保留其特性,一直是覆铜板业内人士极为关注的问题,人们尝试过各种改性双氰胺方法,制出各种双氰胺衍生物,让其保留双氰胺特性,消除双氰胺缺陷,这些制品虽未有商品化产品供广大覆铜板厂应用,但相信各覆铜板厂在产品性能改进或新产品开发时,都会去研究这一课题的。
环氧玻纤布覆铜板使用促进剂,当前多数使用2-甲基咪唑或苄基二甲胺。有人分析,对比数种环氧树脂固化促进剂以后,认为在下列数种固化促进剂:2-甲基咪唑(2MZ)、2-乙基4-甲基咪唑(2E4MZ)、2-苯基咪唑(2PZ)、2-苯基4-乙基咪唑(2P4MZ),在环氧树脂/双氰胺体系中,固化物的固化速度为:2MZ>2E4MZ >2PZ>2P4MZ;固化物的Tg为:2PZ >2P4MZ>2E4MZ>2MZ;树脂溶液及粘结片贮存时间为:2P4MZ>2PZ>2E4MZ>2MZ;在高温下升华量为:2MZ>2E4MZ>2PZ>2P4MZ。上述这些分析对比性结论,在产品性能改进或新产品开发时,有一定参考价值。
|